What to Do When Problems Occur During Coating Application? – Solution Analysis
Coating systems are widely used in fields like steel structures and mechanical equipment, primarily for protection and aesthetics. However, coating systems often fail during use, resulting in issues such as cracking, detachment, and corrosion. This not only affects the appearance but may also cause damage to the substrate. The causes of coating failure are varied, involving environmental factors, construction processes, and more. This article will analyze common causes of coating failure and explore effective solutions to enhance the durability and functionality of coating systems.
1. Adhesion Failure/Detachment/Peeling off
Peeling: Loss of adhesion between the coating and the substrate or between different coating layers.
Possible causes: Surface contamination or condensation on the surface.
Prevention: 1. Ensure the surface is clean, dry, and free of contaminants; 2. Proper surface treatment; 3. Correct matching construction.
Repair: Remove defects according to the extent of peeling and perform appropriate surface treatment; use the correct coating system as recommended by the manufacturer.
2. Dry Spray
Dry Spray: Coating particles fail to flow properly, resulting in rough and uneven finishes, with poor adhesion.
Possible causes: 1. Incorrect spraying technique, such as improper gun distance; 2. Fast-drying products (solvent evaporates too quickly); 3. High temperatures during application; 4. High wind during spraying.
Prevention: 1. Use correct spraying equipment and technique; 2. Use slower-drying solvents; 3. Spray in suitable environmental conditions; 4. Follow recommended construction procedures.
Repair: Before the coating cures or dries: Remove mist with a dry brush and wipe with solvent; After curing or drying: Sand and recoat.
Dry Spray condition performance:
3. Pinholes – Small and Deep Holes
Pinholes: Small holes formed in the wet film due to the expansion of air or solvent gases mixed into the coating during application and drying. The holes do not close before the coating dries.
Possible causes: 1. Solvents or air trapped in the coating; 2. Pinholes are more likely when applying coatings over porous surfaces, such as inorganic zinc coatings or metal spray surfaces; 3. Incorrect spraying techniques and inappropriate solvents can also cause pinholes.
Prevention: 1. Use correct application procedures and select appropriate coating systems; 2. Use suitable solvents and work in optimal environmental conditions; 3. Check spraying equipment and maintain proper distance between the spray gun and surface.
Repair: Sand, clean, and apply an appropriate sealer/primer and topcoat.
4. Runs & Sags
Runs & Sags: The coating is applied too thickly, causing it to move downward or flow like tears when applied to vertical surfaces. Sometimes it may resemble a waterfall.
Possible causes: 1. Excessively thick coating; 2. Too much solvent; 3. Incorrect or lack of hardener; 4. Extreme environmental conditions (too cold or too hot) can cause runs and sags.
Prevention: Use the correct coating system, follow proper application techniques, and choose the right dry film thickness.
Repair: 1. Remove runs before the coating dries using a brush or roller; 2. Once dried, sand, clean, and recoat or patch as necessary.
5. Bleaching/Fading
Bleaching/Fading: The coating loses part or all of its original color.
Possible causes: Bleaching: Caused by atmospheric exposure or chemical attack; Fading: Caused by atmospheric exposure and ultraviolet rays.
Prevention: Use color-stable pigments/UV-resistant or chemically resistant coatings.
Repair: Remove faded coating or sand and recoat with a more suitable coating system.
6. Chalking
Chalking: A fragile powdery layer forms on the surface of the coating, which may also show discoloration or fading. The speed of chalking depends on the concentration of pigments and the type of resin used. Chalking is a characteristic of certain coatings, such as epoxy coatings.
Possible causes: Exposure to the atmosphere and/or UV rays causing the resin in the coating to degrade.
Prevention: Use suitable topcoats that are resistant to chalking and UV degradation.
Repair: Sand or lightly sand the surface to remove all chalky deposits and loose material, then recoat with a chalk-resistant topcoat.
7. Bleeding (Bleed-through)
Bleeding: The diffusion process of colored substances from the underlying substrate or coating film into and through the upper layer of the coating, resulting in an undesirable coloration or discoloration of the coating.
(The image shows tar epoxy bleeding through yellow vinyl coating)
Possible Causes: The soluble colored substances from the underlying layer diffuse to the surface of the topcoat, causing it to lose its original color (especially tar bleeding).
Prevention: Do not use primers containing asphalt/tar in decorative areas.
Repair: Sand down and re-coat with a more suitable coating system.
8. Blistering
Blistering: Dome-shaped protrusions or bubbles on the dried coating surface caused by local loss of adhesion between the surface coating and the underlying layer, which may contain liquid, gas, or crystals inside.
Possible Causes:
1. Grease, salt, rust, trapped moisture, residual solvent, or hydrogen.
2. Local contamination caused by pressure (using cathodic protection), soluble pigments, etc.
3. Loss of adhesion.
4. Blistering can also occur under submerged conditions due to penetration.
Figure (3) Cause of blistering in submerged areas - concentration gradient reaction.
5. Overcurrent protection can also cause blistering.
Figure (2) External current protection Figure (3) Sacrificial anode protection
Prevention: 1. Ensure proper surface preparation and coating application. 2. Use an appropriate coating system. 3. Employ proper cathodic protection.
Repair: Remove the blistered area or the entire coating system depending on the size and type of blister, and patch or re-coat.
9. Bubbles or Bubbling
Bubbles: Small, dome-shaped hollow bodies raised above the coating surface. Bubbles may be intact or ruptured. They are often found on particularly thick coatings, especially in spray or roller applications, but should not be confused with blistering.
Possible Causes: 1. Air/solvent trapped within the coating before surface drying. 2. High viscosity of the coating during roller application. 3. Use of incompatible solvents. 4. Improper mixing and unskilled application. 5. Two-component coatings exceeding the usable time limit after mixing.
Demonstration Principle:
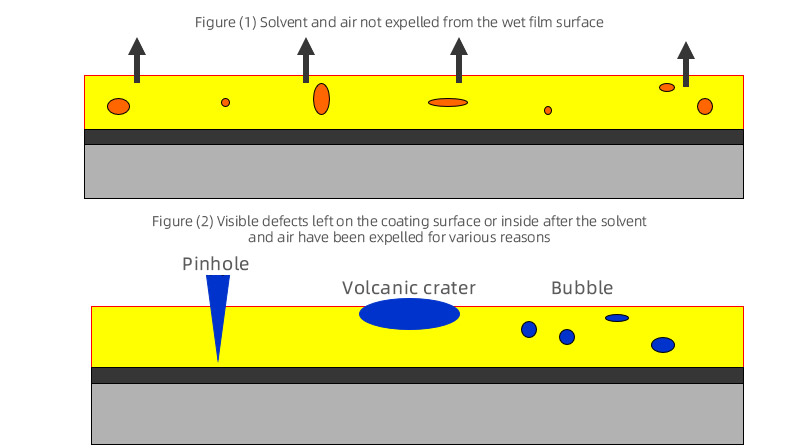
The image above shows solvent and air trapped outside the wet film.
The image below shows visible defects on the coating surface or inside the coating after solvent and air escape for various reasons.
Prevention: 1. Choose the appropriate application method and coating thickness based on the type of coating. 2. Thin the coating to achieve a viscosity suitable for brushing. 3. Apply within the recommended usage time.
Repair: Sand the surface thoroughly based on the distribution and severity, and re-coat with a suitable viscosity coating.
10. Bloom/Blush/Amine Sweating
Amine Sweating: A mist-like deposit on the coating surface, similar to the layer of fruit bloom on grapes, causing the coating surface to lose gloss and darken.
Possible Causes: During curing or drying, the coating is exposed to water vapor condensation, humidity, or low temperatures; or poor ventilation; incorrect solvent mixing may also cause blooming. Blooming/Blush: Formation of ammonium sulfate on the coating surface due to sulfur dioxide and ammonia. Amine sweating and Carbonisation: Reaction of amines, carbon dioxide, and water vapor forming ammonium carbonate.
Prevention: Apply and cure coatings under proper environmental conditions or as recommended by the coating manufacturer.
Repair: Remove the bloom with warm water or an appropriate solvent. Reapply intermediate/topcoats as recommended by the coating manufacturer.
11. Brush Marks
Brush Marks: When brushing, the coating does not level out properly, leaving unsightly, uneven streaks and wrinkles after drying.
Possible Causes: 1. The viscosity of the coating may be too high during brushing. 2. Use of incorrect solvent. 3. Inadequate mixing and unskilled application. 4. Two-component coatings may exceed the usable time limit after mixing.
Prevention: Choose the appropriate brushing method and coating thickness based on the type of coating. Thin the coating to the appropriate viscosity for brushing. Apply within the recommended usage time.
Repair: Sand the surface thoroughly based on the extent of brush marks and re-coat with a coating of suitable viscosity.
12. Fine Cracking (Checking) — No Bare Substrate
Fine Cracking: Small cracks that do not penetrate the topcoat of the coating system. Some cracks are so fine they cannot be seen without a magnifying glass.
Possible Causes: 1. Typically due to coating formula and/or incompatible coatings. 2. Stress accumulation in the coating, making it brittle and causing cracks. 3. Poor coating plasticity.
Prevention: Use the correct formulation for the coating system.
Repair: Sand and clean the coating surface, then apply the appropriate intermediate/topcoat.
13. Cracking (Crazing) — Bare Substrate Visible
Cracking: Visible cracks on the coating surface, potentially penetrating the substrate. Cracking can range from light to severe and may appear in various forms.
Possible Causes: Cracking may be caused by severe stresses or chemical reactions in the coating, substrate movement, aging, moisture absorption and release, and a lack of coating plasticity. The thicker the coating, the greater the likelihood of cracking.
Prevention: Use the correct coating system, proper application techniques, and proper dry film thickness. Use coatings with better plasticity.
Repair: Sand and remove all cracked coatings, and properly reapply the coating system or use coatings with better plasticity and reduced cracking tendency.
14. Softening/Cheesiness
Softening: The coating remains soft even after prolonged drying time.
Possible Causes: 1. Incorrect mixing ratio for two-component coatings. 2. Too low drying/curing temperature. 3. Excessive solvent residues in the coating.
Prevention: Ensure correct mixing ratios; use only the recommended amount of thinner; apply and cure coatings in a controlled environment.
Repair: Remove all soft coatings and apply the appropriate coating system as recommended by the coating manufacturer.
15. Wrinkling (Wrinkling—Rivelling—Crow’s Footing)
Wrinkling: The formation of wrinkles during the drying process of the coating.
Possible causes: 1. Usually caused by the rapid drying of the coating’s surface while the solvent inside evaporates more slowly; 2. Or caused by the strong solvent in the topcoat softening the previous coat and evaporating more slowly; 3. Recoating before the previous coat has completely cured.
Prevention: 1. Use the correct coating system; 2. Correct application techniques and proper dry film thickness; 3. Follow the recoat interval recommended by the coating manufacturer.
Repair: Sand down and remove the wrinkled coating surface, then recoat.
16. Orange Peel
Orange Peel: The surface of the coating is uneven, resembling the peel of an orange.
Possible causes: 1. Poor leveling of the coating (coating too thick or temperature too low); 2. Poor atomization of the coating; 3. Fast evaporation of the solvent; 4. Spray gun too close to the substrate; 5. Unskilled spraying application, or improper solvent mixing.
Prevention: Use correct application techniques and choose a suitable coating system formulation.
Repair: For decorative areas, sand down, clean, and recoat.
17. Cissing/Fisheyes
Description: Cracking of the wet film surface, with the coating retracting and exposing the substrate underneath. The coating does not wet the substrate. The size can be quite large.
Possible causes: 1. The surface is contaminated with moisture or other foreign substances such as oil, grease, and silicone resins; 2. Incorrect solvent compounds used.
Prevention: Ensure the surface is clean and free of grease or other contaminants.
Repair: Sand down and thoroughly clean the surface; or remove the affected coating to achieve a clean surface. Recoat according to the manufacturer's recommendations.
18. Cratering
Description: Small bowl-shaped depressions on the coating surface. Do not confuse with cissing.
Possible causes: 1. Trapped air or solvent bubbles in the coating during drying, leaving small craters; 2. The coating didn’t have enough time to flow out and form a smooth film.
Prevention: 1. Improve spraying technique, apply mist coats, and avoid trapping air during mixing; 2. Follow the coating manufacturer’s recommendations on thinning.
Repair: Sand down and clean the surface, then recoat.
19. Cold Flow
Cold Flow: Caused by the coating not fully curing, resulting in plastic deformation due to water pressure and friction. It may cause unevenness or peeling of the coating.
Possible causes: 1. The coating has not dried/cured, and it was exposed to water or friction too soon.
Prevention: Ensure the coating is fully dried and has enough time to cure, especially during winter.
Repair: Recoat.
20. Dust Particles
Dust Particles: Raised particles on the coating surface that attach to the film before it dries.
Possible causes:
1. Environmental factors: ① Poor air cleanliness in the spraying environment, with dust, fibers, etc.; ② Poor air circulation, excessive mist; ③ Too high a spraying temperature or fast solvent evaporation;
2. Equipment and machinery: ④ Insufficient spraying pressure, poor atomization; ⑤ Poor spray gun cleaning;
3. Material-related issues: ⑥ Contaminated or poorly dispersed coating material;
Prevention: Regular cleaning of the spraying room, drying room, and the ventilation system. Make sure the environment is dust-free. Ensure proper filtration of the coating system.
Repair: 1. Sand down large particles and perform local repairs; 2. Polish small particles after sanding.
References:
1. (GB 5206.5+ FITZ'S ATLAS 2) Color Paints and Varnishes, Vocabulary Part 5; Coatings and Coating Defect Terminology;
2. Steel Structure Construction Quality Acceptance Standards GB 50205-2020;
3. Container Coating Inspection Methods and Acceptance Standards JH/t E04-2008.