Wind Energy Anti-Corrosion Solve
Experts from Mengneng Coatings discussed the types of corrosion faced by offshore wind turbines, including seawater corrosion, marine microorganism corrosion, fatigue corrosion, stress corrosion, and biofouling corrosion. They also proposed corrosion protection measures such as material selection, surface coatings, regular maintenance, electrochemical protection, and antifouling coatings to slow down corrosion and improve the durability of the equipment.
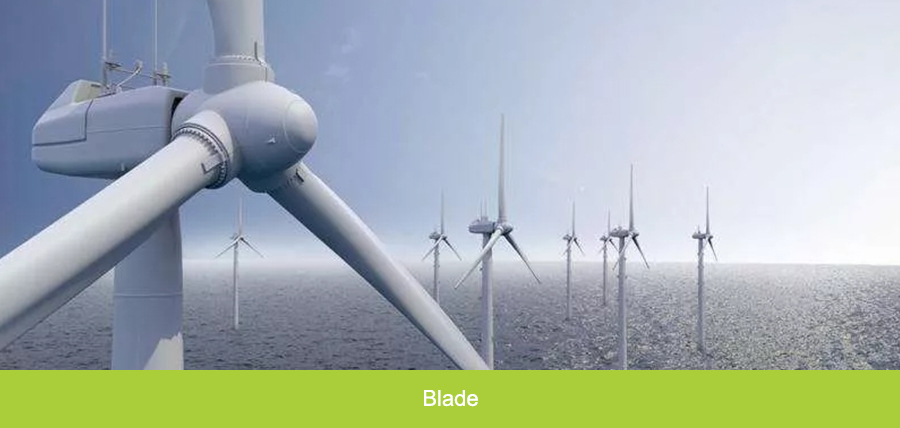
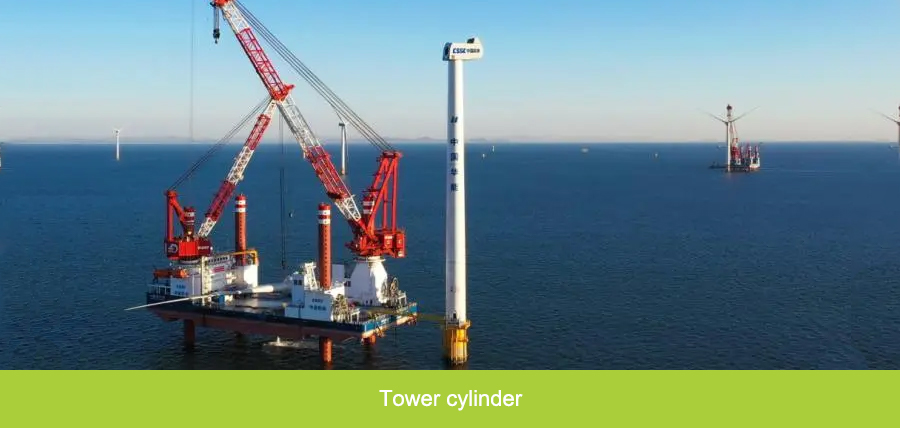
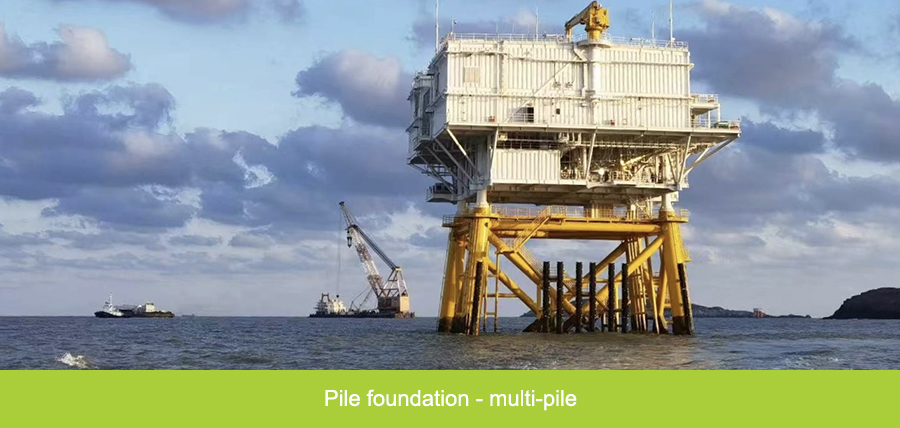
-
Wind Power Corrosion
-
Design Basis
-
Wind Turbine Blades
-
Pile Foundation
-
Tower Shell
-
Nacelle
-
Boosting Station
-
Operation and Maintenance
-
- Corrosion in offshore wind power
-
I. Offshore Wind Power Prospects
In recent years, the construction of offshore wind power projects has been progressing rapidly. The government has introduced a series of policies to support the development of the offshore wind power industry. For example, the "14th Five-Year Plan for Renewable Energy Development," the "14th Five-Year Plan for Modern Energy System," and the "Opinions on Improving the Energy Green and Low-Carbon Transformation System, Mechanism, and Policies" emphasize the need to balance both onshore and offshore wind power development, promoting the coordinated and rapid growth of wind power, improving the offshore wind power industry chain, and encouraging the establishment of offshore wind power bases. Offshore wind power, as an emerging marine industry, has a promising development outlook.
Compared to onshore wind power, offshore wind power faces severe corrosion challenges due to its harsh marine environment, including high humidity, high salt mist, long sunlight exposure, seawater, sea mud, floating debris, and sea ice. Therefore, offshore wind turbines generally have a design life of more than 25 years, and their anti-corrosion design life should exceed 25 years as well. The corrosion control systems must also withstand various environmental tests, such as sea mud, seawater, wave splashing, marine atmosphere, and continuous mechanical damage and wear.
II. Corrosive Environment of Offshore Wind Power
The corrosive environment of offshore wind power is harsh, and its corrosion areas can be divided into: marine atmospheric zone, splash zone, tidal zone, fully submerged zone, and sea mud zone.
1. Marine Atmospheric Zone
The evaporation of seawater forms a high-salinity, high-humidity marine atmosphere, where salts and water films can accumulate on the surface of steel structures. Due to the presence of a small amount of carbon atoms in the steel composition, numerous electrochemical cells can easily form, promoting electrochemical corrosion. The corrosion grade is CX level according to ISO 12944, and the corrosion rate is 4-15 times higher than the atmospheric corrosion rate in inland areas. Not all offshore wind turbines are fully exposed to the CX environment. Through anti-corrosion structural design, the corrosion level of internal areas can be reduced.
2. Splash Zone and Tidal Zone
Both the splash zone and tidal zone are areas with alternating wet and dry conditions, where the salt content on the surface is higher than in the atmospheric zone, and the oxygen content in seawater is higher than in the fully submerged zone. Additionally, the seawater contains mud and floating debris that impact and scrape the surfaces, making these zones the most aggressive corrosion environments. The typical corrosion rate is 0.3-0.5 mm/year, and it can be as high as 1 mm/year, about 3-10 times higher than in the fully submerged zone.
3. Fully Submerged Zone and Sea Mud Zone
In the fully submerged zone, facilities are immersed in seawater for extended periods, and corrosion is influenced by factors such as seawater salinity, seawater temperature, dissolved oxygen concentration, water pollutants, and marine organisms. As shown in Figure 1, a corrosion peak occurs in the fully submerged zone below the average low tide level, while a corrosion minimum occurs above the average low tide level. This is because the steel surface above the waterline receives more oxygen than the steel surface below the waterline, forming an oxygen concentration differential corrosion cell, with the oxygen-rich area acting as the cathode and receiving varying degrees of protection. The relatively oxygen-deprived area serves as the anode, resulting in a significant corrosion peak. The sea mud zone consists of saturated seawater soil, which has high salinity, low resistivity, and insufficient oxygen supply, and also experiences chemical and biological corrosion from the soil.
III. Corrosion Protection Coatings Design for Offshore Wind Power
Experts from Mengneng Coatings believe that the corrosion environment for offshore wind power is complex. The corrosion protection of offshore wind turbines is a systematic issue. For each part of the turbine, corrosion protection should first be considered in terms of structural design and material selection, followed by further enhancement with protective coatings. To ensure the safe operation of wind power facilities and achieve a service life of over 25 years, a reasonable coating system should be designed based on the corrosion characteristics of each part.
Mengneng’s heavy-duty anti-corrosion coatings are widely used in numerous offshore wind farms. We have participated in multiple domestic offshore wind power projects, providing corrosion protection for offshore wind turbine blades, towers, booster stations, and pile foundation components in several wind power projects. Our high-quality products and services have been widely recognized by the market and customers.
IV. Coating Process
The corrosion protection process for wind turbine towers includes four steps: environmental control, surface treatment, coating application, and quality control. By removing oxides, oils, and dirt, selecting suitable epoxy or polyurethane coatings for layering, conducting quality inspections, and promptly detecting and repairing coating issues, the corrosion protection effect for wind turbine towers can be achieved, ensuring safe and reliable operation.
4.1 Environmental Control
This mainly includes temperature, humidity, and dew point temperature. During the coating process, the environmental temperature should be above 5°C. Low temperatures affect curing and increase viscosity, requiring the addition of a thinner. High temperatures cause solvent evaporation too quickly, which can lead to defects in the film. Relative humidity should be ≤ 85%, as higher humidity can affect drying. When applying polyurethane coatings, fluorocarbon coatings, etc., relative humidity should be controlled below 80% to avoid surface blooming. The surface temperature of steel substrates should be at least 3°C higher than the dew point temperature, and surface condensation must be avoided.
4.2 Surface Treatment
Contaminants such as oil, water, dust, salt, and rust on steel surfaces can affect the adhesion and corrosion resistance of coatings. Therefore, thorough surface treatment of the substrate is required. The surface treatment of tower substrates includes degreasing, salt removal, rust removal, and sandblasting. Before sandblasting, special cleaning agents should be used to remove all oils, followed by rinsing and drying before the sandblasting process. After sandblasting, all dust and residual sand must be removed from the substrate surface, and the surface cleanliness and roughness should be checked, typically to ISO 8501-1 Sa2.5 standards. After surface treatment, the substrate should be clean, dry, and free of grease, and the first primer should be applied as soon as possible, preferably within 4 hours of treatment. If the steel surface rusts or becomes contaminated, it must undergo surface treatment again before further coating can proceed.
4.3 Coating Application
The coating should be applied in a well-ventilated indoor environment, avoiding the impact of sand and dust on the application process. Coating process documents and instructions should be carefully reviewed. The application should strictly follow the design process requirements, with coating intervals in line with product technical specifications. Before application, coatings should be thoroughly mixed with an electric or pneumatic mixer until uniform. High-pressure airless spraying is used for large-area component applications, while brushing and rolling are suitable for small areas or pre-coating and minor repairs.
4.4 Quality Control
The coating contractor should establish a coating quality control program and build a complete quality control system. Instruments such as a thickness gauge, hygrometer, dew point meter, surface roughness tester, adhesion tester, and salt tester, along with effective coating standards and specifications, should be utilized.
1) Appearance: The coating surface should be smooth, with uniform color and thickness, and free of obvious defects such as pinholes, runs, whiteness, shrinkage holes, contamination, or missed spraying.
2) Thickness: The wet film thickness of each coating should be immediately measured after application using a wet film thickness gauge to ensure that the final dry film thickness meets design requirements. The dry film thickness should be checked with a magnetic thickness gauge, and if insufficient, the coating should be reapplied. The average dry film thickness of each layer should meet the minimum required dry film thickness and should not exceed the maximum specified thickness.
3) Adhesion: A pull-off adhesion test should be conducted, with adhesion ≥ 5 MPa. Since interlayer adhesion tests are destructive, it is recommended not to perform the test on components but to conduct the test on samples applied alongside the components. After complete curing, the test should be conducted on the samples.
4) Conclusion: Today, the country is strengthening ecological environmental protection. With technological advancements and clear policy guidance, China’s wind power industry is expected to mature and further develop, though it faces significant challenges. Mengneng has developed new wind power coatings and application processes tailored to the actual operational environment of wind power equipment, breaking the market and technological monopoly of foreign imports. With the continued expansion and demand for domestic tower coatings, new opportunities for growth will emerge.
-
How to Select the Right Coating Type?
We don't know where to start.
-
ISO 12944 is a standard developed for corrosion protection of steel structures by paints, determining the corrosive environment, anti-corrosion life, paint matching, and film thickness.
Choose
-
How to Solve Industry with Coatings?
Corrosion factors are numerous and varied.
-
We serve municipal engineering, chemical industry, power plants, steel structure factories, and wastewater treatment plants, with numerous successful cases and experience.
Experience