Industrial Valve Anti-Corrosion Solve
Valves are commonly used components in industrial production. In pipeline installation and chemical pump installation, valves are essential control devices. There are many types of valves, and the valves used in industrial production usually have corrosion resistance. Liquid corrosion is the destruction and deterioration of materials under various environmental conditions. Metal corrosion is mainly caused by chemical corrosion and pitting chemical corrosion, while corrosion of non-metallic materials is generally caused by direct chemical and physical actions. Corrosion is one of the main factors leading to valve damage. Therefore, corrosion protection is the primary consideration in the use of valves.
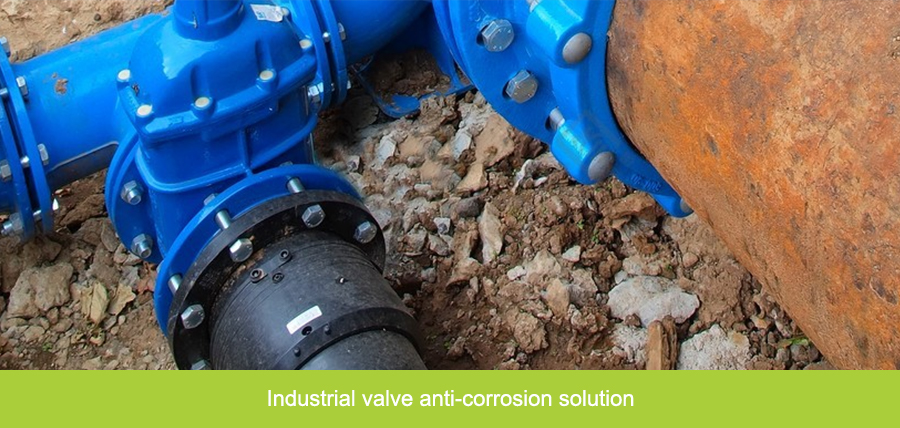
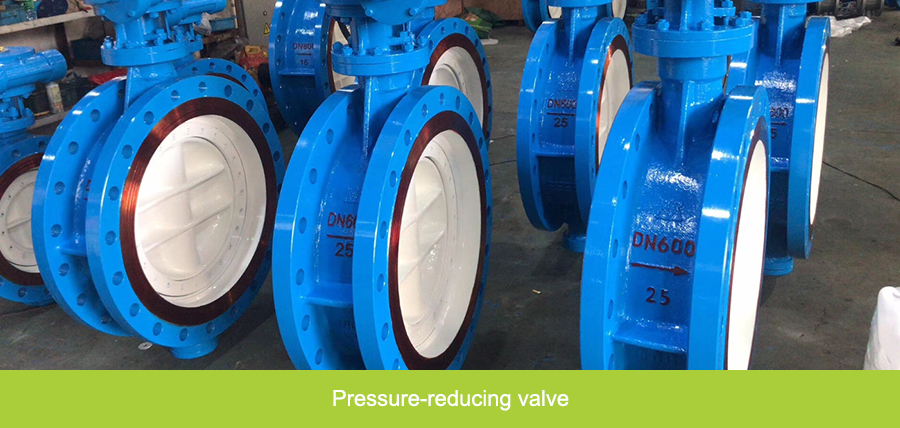
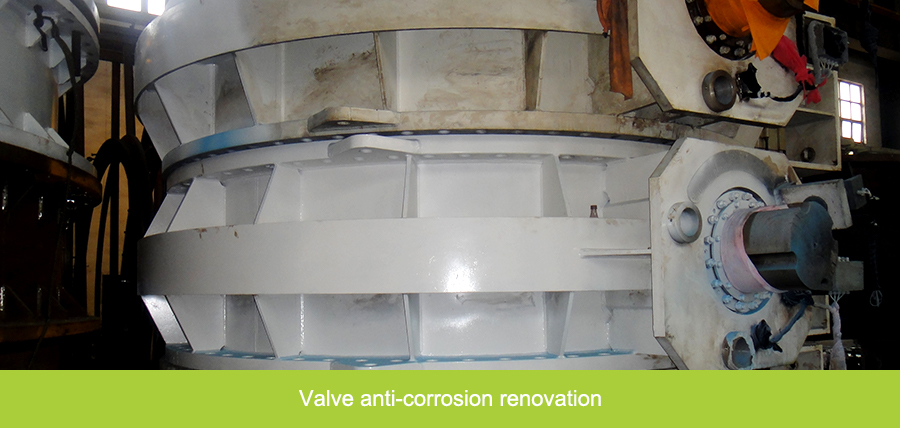
-
Corrosion Background
-
Design Basis
-
Butterfly Valves
-
Ball Valves
-
Regulating Valves
-
Gate valve
-
Globe Valves
-
Check Valves
-
- Corrosion Background of Industrial Valves
-
I. Industrial Valve Corrosion Background
Industrial valves are important components in industrial pipelines, used to control the flow of various media such as air, water, steam, various corrosive substances, slurry, oil, molten metals, and radioactive media. Valve corrosion is typically understood as the degradation of the valve's metallic materials due to chemical or electrochemical environmental factors. Metal corrosion has a significant impact on the valve's operational lifespan, reliability, and service life.
The combined effects of mechanical and corrosive factors greatly increase the overall wear on the contact surfaces. During operation, the valve's friction surfaces experience wear due to the simultaneous mechanical action and the chemical or electrochemical interaction between the metal and the environment, leading to wear and damage. For valves, the complexity of climatic conditions and the presence of hydrogen sulfide, carbon dioxide, and certain organic acids in media such as oil, natural gas, and oilfield water exacerbate the destructive impact on metal surfaces, causing them to lose their functionality quickly.
-
- Reference Standards
-
I. Reference Standards
Current national standards, relevant regulations, and mandatory standard provisions;
"Code for Construction and Acceptance of Building Anti-corrosion Engineering" (GB50212-2002)
"Standard for Corrosion and Rust Removal Levels of Steel Surface Before Coating" (GB8923-1988)
"Safety Regulations for Coating Operations and Safety Management Rules" (GB6514-1995)
"Quality Requirements for Anti-corrosion Coatings" (GB6514-1991)
"Safety Regulations for Coating Operations, Paint Process Safety, and Ventilation Purification" (DJ/T6931-1999)
"Code for Construction and Acceptance of Industrial Equipment and Pipeline Anti-corrosion Engineering" (HGJ229-91)
"Safety Regulations for Coating Operations and Safety of Surface Preparation Process" (GB7692-87)
"Noise Limits at Construction Sites" (GB12523-90)
ISO9001 Quality Management System Documents
ISO14001 Environmental Management System Documents
GB/T28001 Occupational Health and Safety Management System Documents
- Design Basis
-
I. Design Basis
Environmental Conditions: The corrosion level of atmospheric environments on steel structures can be determined according to Table 1.
Atmospheric Corrosivity Classification and Typical Environmental Cases Corrosivity Level Mass and Thickness Loss per Unit Area (After one year of exposure) Typical Environmental Cases in Temperate Climate (For Reference Only) Carbon Steel Zinc External Internal Mass Loss Thickness Loss Mass Loss Thickness Loss /g·m2 /um /g·m2 /um C1 Very Low ≤10 ≤1.3 ≤0.7 ≤0.1 / Interior of heated buildings with clean air, such as offices, shops, schools, and hotels C2 Low >100-200 >1.3-25 >0.7-5 >0.1-0.7 Atmosphere with low pollution level, mostly rural areas Non-heated buildings with potential for condensation (such as warehouses, gyms, etc.) C3 Medium >200-300 >25-50 >5-15 >0.7-2.1 Urban and industrial atmospheres with moderate sulfur dioxide pollution and low salinity coastal areas Production plants with high temperature and some air pollution, such as food processing plants, laundries, wineries, dairy factories, etc. C4 High >400-650 >50-80 >15-30 >2.1-4.2 Industrial areas with medium salinity and coastal regions Chemical plants, swimming pools, coastal ships, and shipyards C5 Very High >650-1500 >80-200 >30-60 >4.2-8.4 Industrial areas with high humidity and harsh weather, and high salinity coastal areas Buildings and areas with condensation and high pollution occurring continuously CX Extreme >1500-5500 >200-700 >60-180 >8.4-25 Offshore areas with high salinity and tropical/subtropical industrial areas with extremely high humidity and aggressive atmosphere Industrial areas with extremely high humidity and corrosive atmosphere Note: The loss values used to define the corrosivity levels are the same as those given in ISO 9223.
-
- Butterfly Valve Inner Wall Anti-corrosion Solution
-
I. Butterfly Valve Corrosion Protection Scheme
Corrosion is a common problem encountered during the use of butterfly valves and is also a manifestation of valve material damage caused by environmental or other factors. Since the corrosion of butterfly valves is triggered by factors such as the environment, to achieve corrosion protection for the butterfly valve, measures must be taken from both the environment and the valve itself. In a butterfly valve, the valve body accounts for a significant proportion, making the corrosion of the valve more severe during the corrosion process. The causes of corrosion are generally divided into two types: chemical corrosion and electrochemical corrosion. The rate of these two types of corrosion depends on the temperature, pressure, and chemical properties of the corrosive medium in the environment, and partly on the inherent chemical properties of the valve body material. Therefore, DreamZinc Technology has developed a corrosion protection scheme using both water-based and oil-based coatings for the butterfly valve corrosion issue.
Table 1: Valve Inner Wall Corrosion Protection Scheme
Design Basis ISO 12944-5:2017 Protective Paint Systems for Steel Structures Environment Im1; Freshwater: Facilities installed in rivers, Hydroelectric power stations Design Life Long-term (H) Surface Treatment ISO 8501-1 Sa2.5: Very thorough abrasive blasting or shot blasting. The steel surface should have no visible grease, dirt, mill scale, rust, paint coatings, or other contaminants. Any residual traces should only be minor specks or streaks. Coating Location Inner wall of the valve Coating Coating Type Coating Name Color Thinner A:B Ratio Film Thickness (μm) First Layer DreamCover DreamZinc Solvent-Free Graphene Coating DreamCover 155 Gns White, Semi-gloss No thinning required 20:5 400 Total 400
-
- Ball Valve Outer Wall Anti-corrosion Solution
-
I. Ball Valve External Corrosion Protection Scheme
Corrosion is a common issue encountered during the operation of ball valves. It is a form of damage caused by environmental or other factors affecting the valve materials. Since the corrosion of ball valves is triggered by external factors like the environment, and considering that the valve body occupies a large proportion of the valve, the degree of corrosion is typically significant. The causes of corrosion are generally divided into two types: chemical corrosion and electrochemical corrosion. The rate of corrosion for both types depends on factors such as environmental temperature, pressure, the chemical properties of the corrosive medium, and to some extent, the inherent chemical properties of the valve body materials. To address this, Mengneng Technology has developed a corrosion protection scheme using water-based and oil-based coatings for ball valves.
Oil-based Coating Corrosion Protection Scheme
Reference Basis ISO 12944 (2017 version) ISO 12944-2017 is a standard compiled by the International Organization for Standardization for those engaged in coating anti-corrosion work, such as owners, designers, consultants, painting contractors, and coating manufacturers, providing a reference for them. Corrosive Environment C3 Moderate Corrosion Location Outdoor Environment Service Life 7-15 years Surface Treatment Thorough manual and power tool rust removal to St2 level (ISO 8501-1:2007), ensuring no visible oil, grease, or contaminants without magnification, and no loose oxide scale, rust, coatings, or foreign impurities. Coating Location Urban and industrial atmospheres, moderate sulfur dioxide pollution, low-salinity coastal areas Coating Coating Type Coating Name Ratio Dry Film First Coat DreamZinc Graphene Zinc Primer DreamZinc 60 Gns 22.5:2.5 75μm Second Coat DreamCover Epoxy Zinc-Rich Intermediate Coat DreamCover 150 22.5:2.5 125μm Third Coat DreamDur Polyurethane Finish Coat DreamDur 550 22.5:2.5 50μm Actual Total Thickness 250μm Water-based Coating Corrosion Protection Scheme
Reference Basis ISO 12944 (2017 version) ISO 12944-2017 is a standard compiled by the International Organization for Standardization for those engaged in coating anti-corrosion work, such as owners, designers, consultants, painting contractors, and coating manufacturers, providing a reference for them. Corrosive Environment C3 Moderate Corrosion Location Outdoor Environment Service Life 7-15 years Surface Treatment Thorough manual and power tool rust removal to St2 level (ISO 8501-1:2007), ensuring no visible oil, grease, or contaminants without magnification, and no loose oxide scale, rust, coatings, or foreign impurities. Coating Location Urban and industrial atmospheres, moderate sulfur dioxide pollution, low-salinity coastal areas Coating Coating Type Coating Name Ratio Dry Film First Coat DreamZinc Cold Spray Zinc DreamZinc 96 10:0 60μm Second Coat DreamCover Cold Spray Zinc Sealing Coating DreamCover 167 10:0 100μm Third Coat DreamDur Polyurethane Finish Coat DreamDur 550 10:0 60μm Actual Total Thickness 220μm
- Ball Valve Inner Wall Anti-corrosion Solution
-
1. Ball Valve Corrosion Protection Plan
Ball valves are widely used in industries such as oil refining, long-distance pipelines, chemicals, paper-making, pharmaceuticals, water, energy, municipalities, steelmaking, and more, playing a vital role in the national economy.
During the use of ball valves, corrosion issues often occur. Typically, corrosion of the valve body is understood as the damage to the metal caused by the chemical or electrochemical effects of the environment. Since the phenomenon of "corrosion" results from the spontaneous interaction between metal and the surrounding environment, the focus in corrosion prevention is on how to separate the metal from the environment or the use of more non-metallic composite materials.
Corrosion Protection Plan Using Oil-Based Coatings
Reference ISO 12944 (2017 Edition) ISO 12944-2017 is an international standard issued by the International Organization for Standardization for owners, designers, consultants, contractors, and manufacturers of coatings. This standard provides reference for these stakeholders. Corrosion Environment Moderate Corrosion C3 Location Indoor Environment Service Life 7-15 years Surface Preparation Complete rust removal by blasting to Sa2.5 level (ISO 8501-1:2007), the surface should be free of oil, grease, and dirt, with no oxides, rust, coatings, or foreign contaminants visible at the inspection level without magnification. Any contamination should only appear as marks or small lines.
Manual rust removal by dynamic tools to St2 level (ISO 8501-1:2007), the surface should be free from oil, grease, and dirt, and without oxides, rust, coatings, or foreign contaminants that are not adhered.Specific Application Site Industrial areas with high humidity and polluted air, such as food processing factories, laundries, breweries, dairy plants, etc. Layer Coating Type Coating Name Ratio Dry Film Thickness First Layer DreamCover DreamCover 350 Water Tank Coating 20:5 100μm Second Layer DreamDur DreamDur 550 Polyurethane Coating 20:5 50μm Total Actual Thickness 150 microns Corrosion Protection Plan Using Water-Based Coatings
Reference ISO 12944 (2017 Edition) ISO 12944-2017 is an international standard issued by the International Organization for Standardization for owners, designers, consultants, contractors, and manufacturers of coatings. This standard provides reference for these stakeholders. Corrosion Environment Moderate Corrosion C3 Location Indoor Environment Service Life 7-15 years Surface Preparation Manual rust removal by dynamic tools to St2 level (ISO 8501-1:2007), the surface should be free from oil, grease, and dirt, and without oxides, rust, coatings, or foreign contaminants that are not adhered. Specific Application Site Industrial areas with high humidity and polluted air, such as food processing factories, laundries, breweries, dairy plants, etc. Layer Coating Type Coating Name Ratio Dry Film Thickness First Layer DreamZinc DreamZinc 60 Gns Zinc Coating 15:3 50μm Second Layer DreamCover DreamCover 150 Epoxy Coating 15:3 100μm Third Layer DreamDur DreamDur 550 Polyurethane Coating 10:0 50μm Total Actual Thickness 200 microns
-
- Regulating Valve Inner Wall Anti-corrosion Solution
-
I. Corrosion Protection Plan for the Inner Wall of the Regulating Valve
A regulating valve, also known as a control valve, is the final control element in industrial automation process control. It adjusts process parameters such as flow rate, pressure, temperature, and liquid level by receiving control signals from the regulating control unit and using power operation. Since the regulating valve directly contacts the medium, it may experience corrosion or wear due to temperature, pressure, viscosity, solid particles, or corrosive media. The corrosion or wear can take many forms, with the valve plug and valve seat being particularly vulnerable to severe corrosion or wear due to high-speed scouring by the medium.
II. Oil-Based Coating Corrosion Protection Plan
Reference Basis ISO 12944 (2017 Edition) ISO 12944-2017 is a standard compiled by the International Organization for Standardization for owners, designers, consultants, coating contractors, and coating manufacturers engaged in anti-corrosion coating work, providing a certain reference for these parties. Corrosion Environment C3 Moderate Corrosion Location Indoor Environment Service Life 7 years to 15 years Surface Treatment Very thorough abrasive blasting to Sa2.5 level (ISO 8501-1:2007). When observed without magnification, the surface should be free of visible oil, grease, and dirt, and there should be no oxide scale, rust, coating, or foreign impurities. Any remaining contamination should only appear as minor spots or streaks.
Thorough hand and power tool cleaning to St2 level (ISO 8501-1:2007). When observed without magnification, the surface should be free of visible oil, grease, and dirt, and there should be no loosely adhered oxide scale, rust, coating, or foreign impurities.Coating Location Production sites with high humidity and some polluted air, such as food processing factories, laundries, distilleries, dairy farms, etc. Coating Coating Type Coating Name Ratio Dry Film Thickness First Coat DreamCover Drinking Water Tank Coating DreamCover 350 20:5 120μm Second Coat DreamDur Polyurethane Finish Coat DreamDur 550 20:5 60μm Actual Total Thickness 180μm III. Water-Based Coating Corrosion Protection Plan
Reference Basis ISO 12944 (2017 Edition) ISO 12944-2017 is a standard compiled by the International Organization for Standardization for owners, designers, consultants, coating contractors, and coating manufacturers engaged in anti-corrosion coating work, providing a certain reference for these parties. Corrosion Environment C3 Moderate Corrosion Location Indoor Environment Service Life 7 years to 15 years Surface Treatment Thorough hand and power tool cleaning to St2 level (ISO 8501-1:2007). When observed without magnification, the surface should be free of visible oil, grease, and dirt, and there should be no loosely adhered oxide scale, rust, coating, or foreign impurities. Coating Location Production sites with high humidity and some polluted air, such as food processing factories, laundries, distilleries, dairy farms, etc. Coating Coating Type Coating Name Ratio Dry Film Thickness First Coat DreamZinc Graphene Zinc Powder Primer DreamZinc 60 Gns 15:3 60μm Second Coat DreamCover Epoxy Micaceous Iron Oxide Intermediate Coat DreamCover 150 15:3 100μm Third Coat DreamDur Polyurethane Finish Coat DreamDur 550 10:0 60μm Actual Total Thickness 220μm
- Regulating Valve Outer Wall Anti-corrosion Solution
-
I. Corrosion Protection Scheme for the Outer Wall of the Regulating Valve
The corrosion damage to metal has a significant impact on the service life, reliability, and longevity of the regulating valve. The mechanical and corrosive factors greatly increase the total wear on the contact surface of the valve. The total wear of the friction surface during the operation of the regulating valve. During operation, the friction surface experiences wear and damage due to simultaneous mechanical action as well as chemical or electrochemical interactions between the metal and the environment. For regulating valves, the climatic conditions of pipeline engineering are complex: the presence of hydrogen sulfide, carbon dioxide, and some organic acids in media such as oil, natural gas, and formation water increases the destructive power on the metal surface, thus quickly impairing its working ability.
Oil-Based Coating Corrosion Protection Scheme
Reference Standard ISO 12944 (2017 Edition) ISO 12944-2017 is a standard compiled by the International Organization for Standardization for those involved in corrosion protection work with coatings, including owners, designers, consultants, coating contractors, and coating manufacturers. It provides a reference for these individuals and organizations. Corrosive Environment C3 Moderate Corrosion Location Outdoor Environment Service Life 7 years to 15 years Surface Treatment Thorough hand and power tool rust removal to St2 level (ISO 8501-1:2007). The surface should be free of visible oil, grease, and contaminants, with no loose oxide, rust, coating, or foreign impurities upon visual inspection without magnification. Coating Area Urban and industrial atmosphere, moderate sulfur dioxide pollution, low salinity coastal areas Coating Layer Coating Type Coating Name Ratio Dry Film Thickness First Layer DreamZinc Graphene Zinc Powder Primer DreamZinc 60 Gns 22.5:2.5 80μm Second Layer DreamCover Epoxy Zinc-Rich Intermediate Coating DreamCover 150 22.5:2.5 120μm Third Layer DreamDur Polyurethane Topcoat DreamDur 550 22.5:2.5 60μm Actual Total Thickness 260 microns Water-Based Coating Corrosion Protection Scheme
Reference Standard ISO 12944 (2017 Edition) ISO 12944-2017 is a standard compiled by the International Organization for Standardization for those involved in corrosion protection work with coatings, including owners, designers, consultants, coating contractors, and coating manufacturers. It provides a reference for these individuals and organizations. Corrosive Environment C3 Moderate Corrosion Location Outdoor Environment Service Life 7 years to 15 years Surface Treatment Thorough hand and power tool rust removal to St2 level (ISO 8501-1:2007). The surface should be free of visible oil, grease, and contaminants, with no loose oxide, rust, coating, or foreign impurities upon visual inspection without magnification. Coating Area Urban and industrial atmosphere, moderate sulfur dioxide pollution, low salinity coastal areas Coating Layer Coating Type Coating Name Ratio Dry Film Thickness First Layer DreamZinc Cold Spray Zinc DreamZinc 96 10:0 60μm Second Layer DreamCover Cold Spray Zinc Sealing Coating DreamCover 167 10:0 120μm Third Layer DreamDur Polyurethane Topcoat DreamDur 550 10:0 50μm Actual Total Thickness 230 microns
-
- Gate Valve Inner Wall Anti-corrosion Solution
-
1. Gate Valve Internal Wall Corrosion Protection Plan
The gate valve has a gate as its closing element, with the movement direction of the gate perpendicular to the flow direction of the fluid. A gate valve can only be fully opened or fully closed, but not used for regulation or throttling. The gate has two sealing surfaces, and the most commonly used type has a wedge-shaped sealing surface, with the wedge angle varying according to the valve parameters, typically 5°, or 2°52' when the medium temperature is low. Corrosion of the gate valve is generally understood as the damage caused to the valve's metal materials due to chemical or electrochemical environments. Since corrosion occurs from the spontaneous interaction between the metal and the surrounding environment, the key to preventing corrosion is isolating the metal from the surrounding environment or using more non-metallic synthetic materials.
Oil-based Coating Corrosion Protection Plan
Reference ISO 12944 (2017 Edition) ISO12944-2017 is a standard compiled by the International Organization for Standardization for owners, designers, consultants, coating contractors, and manufacturers engaged in corrosion protection work, providing a reference for these professionals. Corrosion Environment C3 Moderate Corrosion Location Indoor Environment Service Life 7 to 15 years Surface Preparation Thorough sandblasting to Sa2.5 level (ISO 8501-1:2007). When observed without magnification, the surface should be free of visible oils, fats, and contaminants, and no oxide scale, rust, coatings, or foreign impurities should be present. Any remaining contaminants should appear only as small dots or streaks of minor discoloration.
Thorough hand and power tool cleaning to St2 level (ISO 8501-1:2007). When observed without magnification, the surface should be free of visible oils, fats, and contaminants, and no loose oxide scale, rust, coatings, or foreign impurities should be present.Coating Areas Production areas with high humidity and some polluted air, such as food processing plants, laundries, breweries, dairy farms, etc. Coating Layer Coating Type Coating Name Ratio Dry Film Thickness First Layer DreamCover Drinking Water Tank Coating DreamCover 350 20:5 120μm Second Layer DreamDur Polyurethane Finish Coating DreamDur 550 20:5 60μm Actual Total Thickness 180 microns Water-based Coating Corrosion Protection Plan
Reference ISO 12944 (2017 Edition) ISO12944-2017 is a standard compiled by the International Organization for Standardization for owners, designers, consultants, coating contractors, and manufacturers engaged in corrosion protection work, providing a reference for these professionals. Corrosion Environment C3 Moderate Corrosion Location Indoor Environment Service Life 7 to 15 years Surface Preparation Thorough hand and power tool cleaning to St2 level (ISO 8501-1:2007). When observed without magnification, the surface should be free of visible oils, fats, and contaminants, and no loose oxide scale, rust, coatings, or foreign impurities should be present. Coating Areas Production areas with high humidity and some polluted air, such as food processing plants, laundries, breweries, dairy farms, etc. Coating Layer Coating Type Coating Name Ratio Dry Film Thickness First Layer DreamZinc Graphene Zinc Primer DreamZinc 60 Gns 15:3 60μm Second Layer DreamCover Epoxy Micaceous Iron Intermediate Coating DreamCover 150 15:3 120μm Third Layer DreamDur Polyurethane Finish Coating DreamDur 550 10:0 60μm Actual Total Thickness 240 microns
- Anti-corrosion Solution for Outer Wall of Gate Valve
-
1. Gate Valve Exterior Anti-Corrosion Plan
The corrosion of gate valves is usually understood as the damage caused to the valve's metal materials under chemical or electrochemical environmental effects. Since the chemical corrosion of metals depends on factors like temperature, mechanical load of friction parts, sulfur compounds in lubricants, their acid resistance stability, the duration of contact between metal and medium, the catalytic effect of metals on nitriding processes, and the molecular conversion speed of corrosive substances, DreamEnergy Technology has developed anti-corrosion plans using both water-based and oil-based coatings for gate valve corrosion.
Oil-Based Coating Anti-Corrosion Plan
Reference Standard ISO 12944 (2017 Edition) ISO12944-2017 is a standard compiled by the International Organization for Standardization for owners, designers, consultants, coating contractors, and paint manufacturers engaged in corrosion protection, providing them with a useful reference. Corrosive Environment C4 High Corrosion Location Outdoor Environment Service Life 7 to 15 years Surface Treatment Thorough manual and power tool rust removal to St2 level (ISO 8501-1:2007). When observed without magnification, the surface should be free from visible oil, grease, and dirt, and should not have loosely adhered oxide scales, rust, coatings, or foreign impurities. Coating Location High salinity industrial zones and coastal areas Coating Coating Type Coating Name Mix Ratio Dry Film Thickness First Coat DreamZinc Graphene Zinc Primer DreamZinc 60 Gns 22.5:2.5 80μm Second Coat DreamCover Epoxy Micaceous Iron Intermediate Coating DreamCover 150 22.5:2.5 120μm Third Coat DreamDur Polyurethane Topcoat DreamDur 550 22.5:2.5 60μm Actual Total Thickness 260 microns Water-Based Coating Anti-Corrosion Plan
Reference Standard ISO 12944 (2017 Edition) ISO12944-2017 is a standard compiled by the International Organization for Standardization for owners, designers, consultants, coating contractors, and paint manufacturers engaged in corrosion protection, providing them with a useful reference. Corrosive Environment C4 High Corrosion Location Outdoor Environment Service Life 7 to 15 years Surface Treatment Thorough manual and power tool rust removal to St2 level (ISO 8501-1:2007). When observed without magnification, the surface should be free from visible oil, grease, and dirt, and should not have loosely adhered oxide scales, rust, coatings, or foreign impurities. Coating Location High salinity industrial zones and coastal areas Coating Coating Type Coating Name Mix Ratio Dry Film Thickness First Coat DreamZinc Cold Spray Zinc DreamZinc 96 10:0 80μm Second Coat DreamCover Cold Spray Zinc Sealer DreamCover 167 10:0 100μm Third Coat DreamDur Polyurethane Topcoat DreamDur 550 10:0 60μm Actual Total Thickness 240 microns
-
- Anti-corrosion for the Inner Wall of Gate Valve
-
I. CORROSION PROTECTION FOR THE INNER WALL OF GATE VALVE
A gate valve is a forced-sealing valve primarily used to control the flow of water, air, steam, and various corrosive media, and it has a highly reliable shut-off function. The change in the valve seat opening is directly proportional to the valve disc travel, making it highly suitable for flow regulation. Corrosion of the gate valve manifests in two forms: chemical corrosion and electrochemical corrosion. The corrosion rate is determined by factors such as the medium's temperature, pressure, chemical properties, and the corrosion resistance of the valve body material.
Oil-Based Coating Corrosion Protection Plan
Reference ISO 12944 (2017 Edition) ISO 12944-2017 is a standard compiled by the International Organization for Standardization for owners, designers, consultants, coating contractors, and paint manufacturers involved in corrosion protection through coatings, providing a reference for these personnel and organizations. Corrosive Environment C3 Moderate Corrosion Location Indoor Environment Service Life 7 to 15 years Surface Treatment Thorough hand and power tool rust removal to St2 level (ISO 8501-1:2007). When observed without magnification, the surface should be free from visible oil, grease, and contaminants, and there should be no loosely adhered scale, rust, coatings, or foreign impurities. Coating Area Production environments with high humidity and some polluted air, such as food processing plants, laundries, breweries, dairy farms, etc. Coating Coating Type Coating Name Mixing Ratio Dry Film Thickness First Coat DreamCover Drinking Water Tank Coating DreamCover 350 20:5 120μm Second Coat DreamDur Polyurethane Finish Coating DreamDur 550 20:5 60μm Actual Total Thickness 180 micrometers Water-Based Coating Corrosion Protection Plan
Reference ISO 12944 (2017 Edition) ISO 12944-2017 is a standard compiled by the International Organization for Standardization for owners, designers, consultants, coating contractors, and paint manufacturers involved in corrosion protection through coatings, providing a reference for these personnel and organizations. Corrosive Environment C3 Moderate Corrosion Location Indoor Environment Service Life 7 to 15 years Surface Treatment Thorough hand and power tool rust removal to St2 level (ISO 8501-1:2007). When observed without magnification, the surface should be free from visible oil, grease, and contaminants, and there should be no loosely adhered scale, rust, coatings, or foreign impurities. Coating Area Production environments with high humidity and some polluted air, such as food processing plants, laundries, breweries, dairy farms, etc. Coating Coating Type Coating Name Mixing Ratio Dry Film Thickness First Coat DreamZinc Graphene Zinc Powder Primer DreamZinc 60 Gns 15:3 60μm Second Coat DreamCover Epoxy Micaceous Iron Oxide Intermediate Coating DreamCover 150 15:3 120μm Third Coat DreamDur Polyurethane Finish Coating DreamDur 550 10:0 60μm Actual Total Thickness 240 micrometers
- Anti-corrosion Solution for the Outer Wall of Gate Valve
-
I. Anti-corrosion Protection for the Outer Surface of the Gate Valve
The corrosion of a gate valve is generally understood as the damage caused to the metal material of the valve, such as the V-type regulating ball valve, under the influence of chemical or electrochemical environments. Since the phenomenon of "corrosion" occurs due to the spontaneous interaction between metal and the surrounding environment, the focus of anti-corrosion protection is to isolate the metal from the surrounding environment or to use more non-metallic synthetic materials. The valve body (including the valve cover) accounts for most of the weight of the valve and is in constant contact with the medium, so the selection of the valve is often based on the material of the valve body.
Anti-corrosion Protection Using Oil-based Coatings
Reference Standard ISO 12944 (2017 version) ISO 12944-2017 is a standard compiled by the International Organization for Standardization (ISO) for owners, designers, consultants, coating contractors, and coating manufacturers engaged in corrosion protection. It provides a reference for these professionals and organizations. Corrosive Environment C4 High corrosion Location Outdoor environment Service Life 7 years to 15 years Surface Preparation Thorough manual and power tool rust removal to St2 level (ISO 8501-1:2007). The surface should be free of visible oil, grease, and contaminants, and should not have loose oxide scales, rust, coatings, or foreign impurities when observed without magnification. Coating Location High salt concentration industrial and coastal areas Coating Coating Type Coating Name Mixing Ratio Dry Film Thickness First Layer DreamZinc Graphene Zinc Primer DreamZinc 60 Gns 22.5:2.5 80μm Second Layer DreamCover Epoxy Intermediate Coat DreamCover 150 22.5:2.5 120μm Third Layer DreamDur Polyurethane Finish Coat DreamDur 550 22.5:2.5 60μm Actual Total Thickness 260 microns Anti-corrosion Protection Using Water-based Coatings
Reference Standard ISO 12944 (2017 version) ISO 12944-2017 is a standard compiled by the International Organization for Standardization (ISO) for owners, designers, consultants, coating contractors, and coating manufacturers engaged in corrosion protection. It provides a reference for these professionals and organizations. Corrosive Environment C4 High corrosion Location Outdoor environment Service Life 7 years to 15 years Surface Preparation Thorough manual and power tool rust removal to St2 level (ISO 8501-1:2007). The surface should be free of visible oil, grease, and contaminants, and should not have loose oxide scales, rust, coatings, or foreign impurities when observed without magnification. Coating Location High salt concentration industrial and coastal areas Coating Coating Type Coating Name Mixing Ratio Dry Film Thickness First Layer DreamZinc Cold-spray Zinc DreamZinc 96 10:0 80μm Second Layer DreamCover Cold-spray Zinc Sealing Coat DreamCover 167 10:0 100μm Third Layer DreamDur Polyurethane Finish Coat DreamDur 550 10:0 60μm Actual Total Thickness 240 microns
-
- Anti-corrosion Solution for the Inner Wall of Check Valve
-
I. Check Valve Internal Wall Anti-Corrosion Plan
A check valve is a valve that opens and closes automatically depending on the flow of the medium, primarily used to prevent the reverse flow of the medium. It is also known as a non-return valve, one-way valve, reverse flow valve, and back pressure valve. The check valve is an automatic valve whose main function is to prevent backflow, prevent pump and motor reversal, and prevent the discharge of medium from the container.
Oil-based Coating Anti-Corrosion Plan
Reference Basis ISO 12944 (2017 Edition) ISO 12944-2017 is a standard compiled by the International Organization for Standardization for owners, designers, consultants, coating construction units, and coating manufacturers engaged in corrosion protection work. It provides a certain reference basis for these personnel and units. Corrosive Environment C3 Moderate Corrosion Location Indoor Environment Service Life 7 to 15 years Surface Treatment Thorough hand and power tool rust removal to St2 level (ISO 8501-1:2007). When observed without magnification, the surface should be free of visible oil, grease, and dirt, and should not have loose scale, rust, coatings, or foreign contaminants. Coating Location Production environments with high humidity and some contaminated air, such as food processing factories, laundries, wineries, dairy farms, etc. Coating Coating Type Coating Name Ratio Dry Film Thickness First Coat DreamCover Drinking Water Tank Paint DreamCover 350 20:5 120μm Second Coat DreamDur Polyurethane Topcoat DreamDur 550 20:5 60μm Actual Total Thickness 180μm Water-based Coating Anti-Corrosion Plan
Reference Basis ISO 12944 (2017 Edition) ISO 12944-2017 is a standard compiled by the International Organization for Standardization for owners, designers, consultants, coating construction units, and coating manufacturers engaged in corrosion protection work. It provides a certain reference basis for these personnel and units. Corrosive Environment C3 Moderate Corrosion Location Indoor Environment Service Life 7 to 15 years Surface Treatment Thorough hand and power tool rust removal to St2 level (ISO 8501-1:2007). When observed without magnification, the surface should be free of visible oil, grease, and dirt, and should not have loose scale, rust, coatings, or foreign contaminants. Coating Location Production environments with high humidity and some contaminated air, such as food processing factories, laundries, wineries, dairy farms, etc. Coating Coating Type Coating Name Ratio Dry Film Thickness First Coat DreamZinc Graphene Zinc Powder Primer DreamZinc 60 Gns 15:3 60μm Second Coat DreamCover Epoxy Zinc-Rich Intermediate Paint DreamCover 150 15:3 120μm Third Coat DreamDur Polyurethane Topcoat DreamDur 550 10:0 60μm Actual Total Thickness 240μm
- Anti-corrosion Solution for the Outer Wall of Check Valve
-
I. Check Valve Exterior Corrosion Protection Plan
The corrosion issue of check valves significantly affects the product's service life and can impact its performance. During operation, the valve's friction surfaces experience wear and damage due to mechanical action and chemical reactions. For the valve body, the complexity of the pipeline's working climate conditions, as well as the presence of hydrogen sulfide, certain organic acids in media like petroleum, natural gas, and oilfield water, increases the destructive power on the metal surface, causing it to quickly lose its operational capacity.
Oil-based Coating Corrosion Protection Plan
Reference Standard ISO 12944 (2017 Edition) ISO 12944-2017 is a standard compiled by the International Organization for Standardization for those engaged in corrosion protection coating work, including owners, designers, consultants, coating contractors, and manufacturers, providing them with useful reference. Corrosive Environment C3 Moderate Corrosion Location Indoor environment Service Life 7 to 15 years Surface Treatment Thorough abrasive blasting to Sa2.5 level (ISO 8501-1:2007). When viewed without magnification, the surface should have no visible oil, grease, or contaminants, and no oxide scale, rust, coatings, or foreign impurities. Any traces of contamination should appear as slight spot or stripe discolorations.
Complete manual and power tool cleaning to St2 level (ISO 8501-1:2007). When viewed without magnification, the surface should have no visible oil, grease, or contaminants, and no loosely adhering oxide scale, rust, coatings, or foreign impurities.Coating Area High humidity and moderately polluted air production sites, such as food processing plants, laundries, distilleries, dairies, etc. Coating Coating Type Coating Name Mixing Ratio Dry Film Thickness First Layer DreamCover Graphene Low Surface Treatment Primer DreamCover 220 Gns 20:5 120μm Second Layer DreamDur Polyurethane Topcoat DreamDur 550 20:5 60μm Actual Total Thickness 180 microns Water-based Coating Corrosion Protection Plan
Reference Standard ISO 12944 (2017 Edition) ISO 12944-2017 is a standard compiled by the International Organization for Standardization for those engaged in corrosion protection coating work, including owners, designers, consultants, coating contractors, and manufacturers, providing them with useful reference. Corrosive Environment C3 Moderate Corrosion Location Indoor environment Service Life 7 to 15 years Surface Treatment Complete manual and power tool cleaning to St2 level (ISO 8501-1:2007). When viewed without magnification, the surface should have no visible oil, grease, or contaminants, and no loosely adhering oxide scale, rust, coatings, or foreign impurities. Coating Area High humidity and moderately polluted air production sites, such as food processing plants, laundries, distilleries, dairies, etc. Coating Coating Type Coating Name Mixing Ratio Dry Film Thickness First Layer DreamZinc Graphene Zinc Powder Primer DreamZinc 60 Gns 15:3 60μm Second Layer DreamCover Epoxy Zinc-Rich Intermediate Coating DreamCover 150 15:3 120μm Third Layer DreamDur Polyurethane Topcoat DreamDur 550 10:0 60μm Actual Total Thickness 240 microns
-
How to Select the Right Coating Type?
We don't know where to start.
-
ISO 12944 is a standard developed for corrosion protection of steel structures by paints, determining the corrosive environment, anti-corrosion life, paint matching, and film thickness.
Choose
-
How to Solve Industry with Coatings?
Corrosion factors are numerous and varied.
-
We serve municipal engineering, chemical industry, power plants, steel structure factories, and wastewater treatment plants, with numerous successful cases and experience.
Experience