Wastewater Treatment Anti-Corrosion Solve
The sewage treatment plant has many measures in place. Equipment exposed to air (such as iron tanks), concrete structure pools, pipelines and facilities buried underground, as well as pipelines and equipment in water, are all at risk of corrosion. Although these devices and facilities may not immediately suffer damage when corroded, they are slowly rusting without being noticed. Once the corrosion reaches a certain level, it can suddenly cause rupture, leading to leaks that disrupt production, halt operations, or even cause serious accidents, including casualties. Therefore, regular corrosion checks and maintenance of equipment and facilities should be strengthened. Corrosion issues should be addressed promptly to prevent sudden catastrophic corrosion events.
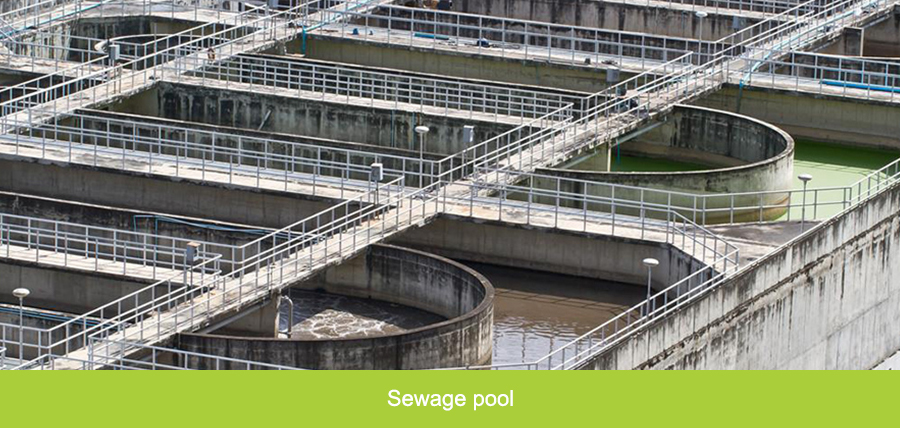
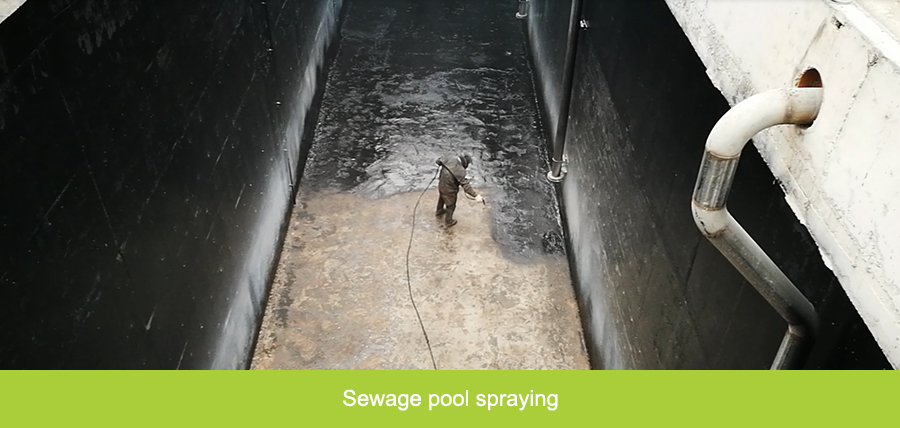

-
Corrosion Background
-
Design Basis
-
Industrial Wastewater Treatment
-
Domestic Wastewater Treatment
-
Aquaculture Wastewater Treatment
-
Electroplating Plant Wastewater Treatment
-
Coating Process
-
- Background of Corrosion Protection in Sewage Treatment
-
Urban sewage, industrial sewage, including wastewater generated from various industries, have different compositions. Even in the same industry, due to differences in processes, the composition of the wastewater can vary, especially with fluctuations in the content of each component. The diversity of wastewater leads to complex changes in the corrosion environment and corrosion patterns of sewage treatment equipment.
Urban sewage is complex, causing severe corrosion to steel equipment such as grids, overflow plates, sludge scraping vehicles, submersible pumps, and railings above the secondary sedimentation tanks. Traditionally, epoxy coal tar coatings have been used for equipment protection, but corrosion often occurs severely within one year of use, even resulting in perforations.
The corrosion media in industrial wastewater treatment systems are especially complex, such as acids, alkalis, salts, and organic substances, which may appear in a mixed or alternating manner. The total amount and concentration of corrosion media are also unstable.
1. Corrosion Factors Facing Concrete
1.1 Concrete Corrosion Protection
The special difficulties of concrete corrosion protection.
The concrete surfaces of pools and tanks in wastewater treatment systems are significantly different from steel surfaces in terms of corrosion protection. Concrete structures have specific requirements for corrosion protection due to their construction characteristics. The surface of the concrete base is loose, rough, porous, and contains microcracks, which pose a major challenge to the adhesion and impermeability of protective coatings.
The moisture content in the concrete base creates certain difficulties for coating protection. The moisture content of the base comes from two sources: first, insufficient hydration of the cement and inadequate curing; second, capillary absorption caused by the high porosity and rough surface. Even if the concrete is fully cured, the absorption of moisture in humid climates may cause an excessive moisture content. Concrete structures are often in a damp state during use, and most of the pools and tanks are in semi-submerged, semi-enclosed environments, creating challenges not only during construction but also during maintenance. Concrete structures, unlike other equipment, cannot be easily repaired or replaced. Once reinforcement corrosion causes concrete cracking, it is difficult to take remedial measures. Many large pools and tanks are constructed in a modular format, where damage in one area can spread to the entire structure, causing serious risks.
1.2 Chemical Corrosion
Carbon dioxide in the atmosphere reacts with calcium hydroxide in cement to form an insoluble carbonate, which blocks the pores of the concrete. Carbon dioxide can also further react with calcium carbonate to form soluble calcium bicarbonate, causing the destruction of concrete.
Concrete structures are inherently alkaline, with a pore liquid pH > 12.5. Alkaline media generally do not cause corrosion to concrete structures, but acids can cause a certain degree of corrosion. Acidic water reacts with Ca(OH)2 to form soluble calcium salts, leading to the deterioration of concrete structures. Sulfuric acid, hydrochloric acid, and nitric acid can decompose calcium silicate and calcium aluminate in the concrete structure, causing surface degradation. When the water is of a sodium carbonate or calcium carbonate type, the calcium carbonate in the water is in an unsaturated state, which can continue to dissolve the carbonate in the concrete, weakening its strength. The higher the temperature of the acidic water, the more severe the corrosion. Long-term exposure to acidic water can react with Ca(OH)2 in concrete to form gypsum, and with calcium aluminate to form ettringite, which leads to the expansion and deterioration of the concrete structure.
1.3 Physical Action
Large reinforced concrete reservoirs are typically constructed outdoors and exposed to seasonal temperature fluctuations, making them susceptible to physical damage such as expansion, cracking, and penetration.
The movement of media can cause surface erosion due to the effect of flow speed, exposing new surfaces and accelerating the corrosion of concrete structures.
The porosity of concrete structures allows corrosive media to enter and be stored in the pores. When dried, crystallization or expansion occurs, increasing the internal stress of the concrete. Repeated cycles of drying and wetting can lead to the destruction of concrete structures.
In wastewater treatment pools made of concrete, freezing expansion can occur. When the water in the pores freezes, its volume increases by 9%, generating significant internal stress, which causes cracks and destruction in the concrete structure. This problem is more prominent in northern regions.
1.4 Microbial Corrosion
The corrosion of concrete structures is most typically manifested by the dissolution and dispersion of hydrates, leading to the expansion and deterioration of the concrete. A microbial film can often be observed on the pool walls of sewage treatment plants. This film attaches to the concrete surface and alters the local pH value and salt concentration, contributing to the corrosion of the concrete.
2. Corrosion Environment of Sewage Pipelines
2.1 Soil Corrosion
The external corrosion of buried pipelines is primarily due to soil corrosion. Soil is a complex mixture of solid, liquid, and gaseous phases, filled with air, water, and various salts, which give it electrolytic properties. Therefore, soil corrosion is the result of the interaction between underground pipelines and the salts or their aqueous solutions in the soil. Corrosion in coastal soil, with its high chloride ion content and sulfate-reducing bacteria, is more severe than that in inland soils. The external corrosion protection of pipelines in such environments requires enhanced protection levels, and a heavy-duty anti-corrosion coating combined with sacrificial anodes is recommended.
A heavy-duty anti-corrosion coating system for buried sewage pipelines can replace oil cloth wrapping, eliminating the need for fiberglass wrapping. It does not have pinhole defects and possesses excellent insulation properties, resistance to microbial erosion, good chemical resistance, strong adhesion, and low water absorption. This coating can be applied directly to steel surfaces with slight rust and is easy to construct with low surface treatment costs and a short construction period.
2.2 Sewage Corrosion
The sewage inside the pipeline contains acids, alkalis, salts, a wide pH range, organic matter, and microorganisms, with high flow velocities. The internal walls of steel pipes not only suffer from the severe corrosion of highly corrosive sewage, but the abrasive effects of high-flow sewage on the pipe wall are also significant. The recommended coating for the interior of pipelines is DreamNeng heavy-duty anti-corrosion graphene epoxy glass flake coating. It is suitable for steel surfaces, offering excellent adhesion, a smooth surface, resistance to salt spray, abrasion, and moisture, as well as excellent resistance to acids, alkalis, salts, oils, and microorganisms. It also has excellent resistance to cathodic delamination and works well with cathodic protection. This coating is widely used for heavy-duty corrosion protection in various steel structures and has a service life of over 15 years in sewage and seawater pipelines.
2.3 Environmental Definition
The corrosion environment for different systems is well defined in international standards like ISO 12944:
From ISO 12944's descriptions of various corrosion environments, the corrosion environment for sewage treatment plant pipelines is defined as follows: Sewage treatment water pipes: should be classified as Im 1 or Im 2, meaning the environment is water corrosion. In fact, the corrosion in sewage treatment plants is stronger than the corrosion levels in ISO 12944. The external walls of sewage treatment water pipes: should be classified as Im 3, indicating soil corrosion.
-
How to Select the Right Coating Type?
We don't know where to start.
-
ISO 12944 is a standard developed for corrosion protection of steel structures by paints, determining the corrosive environment, anti-corrosion life, paint matching, and film thickness.
Choose
-
How to Solve Industry with Coatings?
Corrosion factors are numerous and varied.
-
We serve municipal engineering, chemical industry, power plants, steel structure factories, and wastewater treatment plants, with numerous successful cases and experience.
Experience