Cement Plant Anti-Corrosion Solve
Cement plant equipment is primarily made of metal, and metal materials generally face corrosion issues. Coating, as one of the most important surface protection technologies for cement plant equipment, has been widely adopted by manufacturers. In developed countries, to meet the increasing product requirements and the worsening environmental conditions, the manufacturing and related industries continue to introduce new materials and technologies. This not only ensures that the heavy corrosion protection of cement plant equipment meets the service life requirements, but also ensures that the environmental pollution caused by the coating production process complies with stringent regulatory requirements.
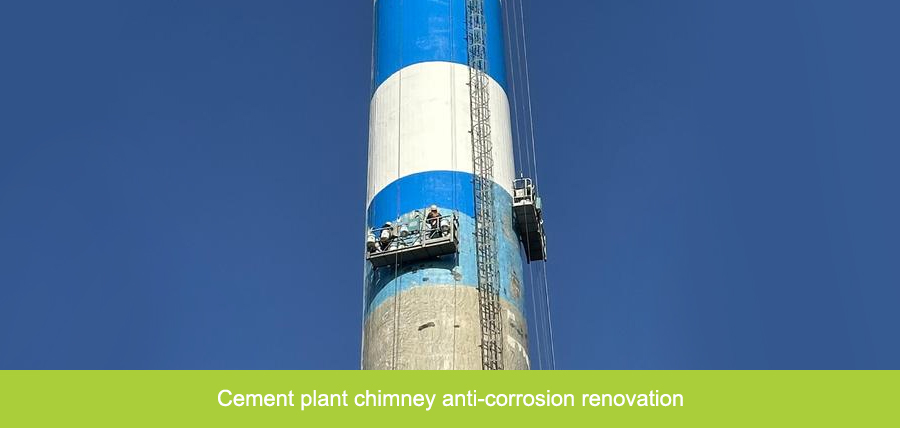
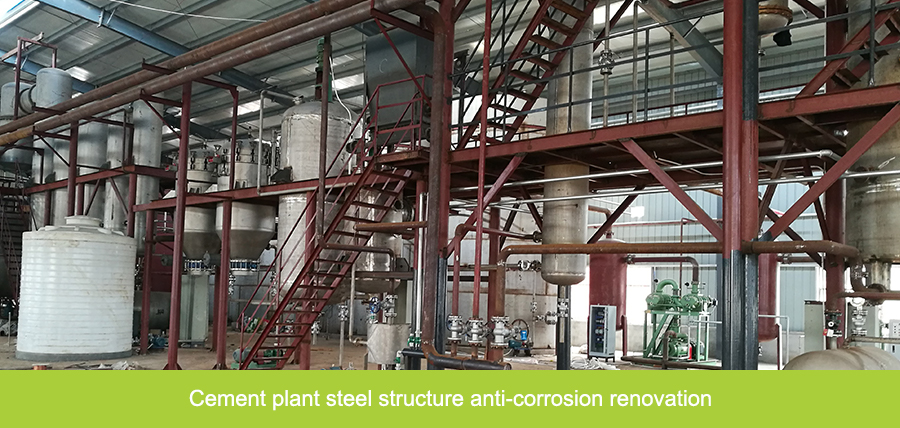
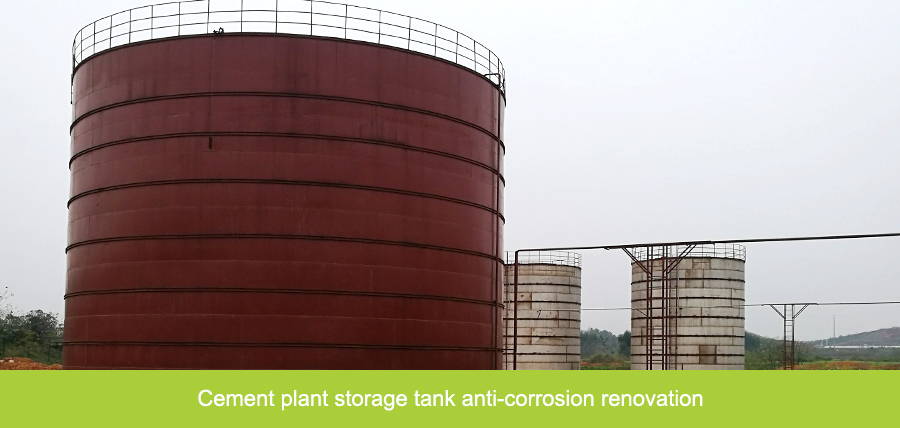
-
Corrosion Background
-
Design Basis
-
Industrial Fans
-
Chimney
-
Preheaters & Decomposing Furnace
-
Lifters
-
Rotary Kiln
-
Bag Dust Collector
-
- Corrosion background in cement plants
-
Causes of Corrosion in Cement Plants:
1) Acid-alkaline corrosion
The pH value of cement dust is about 10-12, which is strongly alkaline, creating an alkaline corrosion environment in the dust collector. Due to the high humidity of flue gas and high dew point temperature, condensation is likely to occur when the temperature of the flue gas drops, especially when there is leakage or other defects in the dust collector. In addition to causing "bag sticking" problems, condensation can also lead to alkaline corrosion of the metal components of the dust collector.
2) High-temperature flue gas corrosion
Flue gas in cement plants typically ranges from 220°C to 350°C (extreme conditions may exceed 400°C). If the dust collector's steel structure is not protected from corrosion and oxidation, the oxidation and corrosion of the metal structure will be severe. Rust and debris from oxidation not only pollute the final product but also cause uneven oxidation and corrosion surfaces that can disrupt the normal flow of flue gas. This can lead to significant dust accumulation in localized areas, severely affecting the normal production of the cement plant.
To ensure that a transformer operates normally over its service life, its outer protective coating system must have good adhesion, weather resistance, water resistance, oil resistance, and heat resistance, as well as excellent corrosion resistance.
3) Ammonia corrosion
During the denitrification process in cement plants, ammonia water is commonly used as a reducing agent. When ammonia water is sprayed in excess, it directly pollutes the equipment. Ammonia has strong adsorption and corrosion properties, and it adheres to equipment such as flue ducts and dust collectors, which is difficult to remove. Over time, it gradually causes corrosion to the equipment. Furthermore, ammonia water decomposes into ammonia gas, which decomposes faster at higher temperatures. Ammonia gas can ionize into ammonium ions and hydroxide ions in a humid environment, forming an electrolytic solution that accelerates the corrosion of metals by promoting electrochemical reactions. Ammonia molecules can form complexes with many transition metal ions, making them easily soluble in water and stripping away the protective oxide layer on the metal surface. During the denitrification process, excessive ammonia water leads to ammonia gas formation, which causes corrosion to metal equipment such as dust collectors and ducts, requiring urgent anti-corrosion measures.
4) Erosion and wear
The flue gas velocity in cement plants is around 1.5 m/s, with a high dust concentration. The erosion and abrasion caused by the flue gas on the metal structures is severe, especially when the flue gas at the kiln head contains larger dust particles. Although the concentration is relatively low, the abrasion is more severe.
-
How to Select the Right Coating Type?
We don't know where to start.
-
ISO 12944 is a standard developed for corrosion protection of steel structures by paints, determining the corrosive environment, anti-corrosion life, paint matching, and film thickness.
Choose
-
How to Solve Industry with Coatings?
Corrosion factors are numerous and varied.
-
We serve municipal engineering, chemical industry, power plants, steel structure factories, and wastewater treatment plants, with numerous successful cases and experience.
Experience