How to Clear?
Mengneng Coating Academy provides comprehensive knowledge on surface preparation before coating. Here, you will learn how to properly clean, remove rust, degrease, and sand to ensure good adhesion and durability of the coating. You will also understand the specific surface treatment methods for different materials and how to choose the appropriate surface treatment chemicals and techniques. Through these courses, you will master key skills to enhance coating performance and extend the service life of the coating.
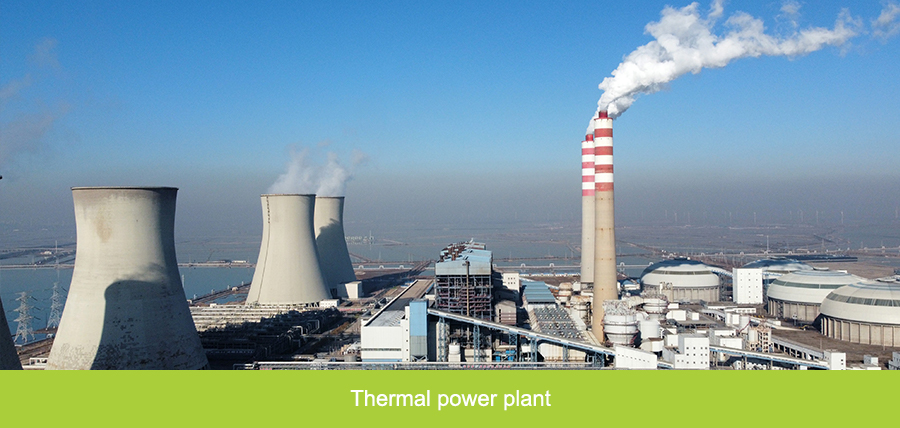
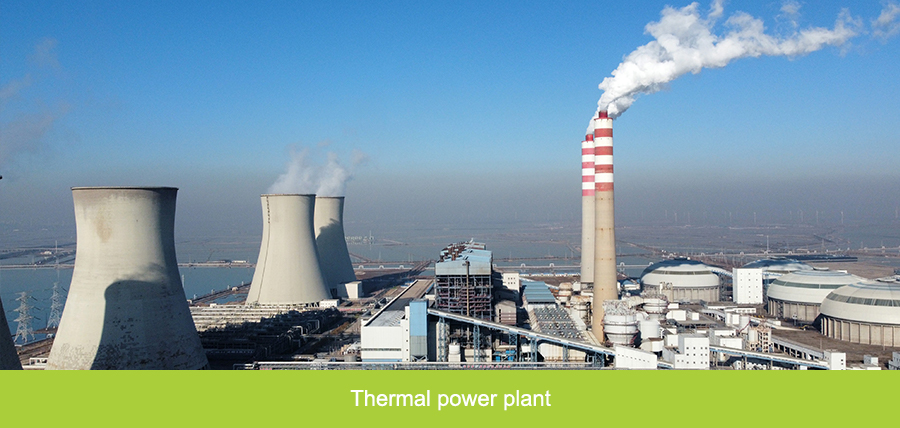
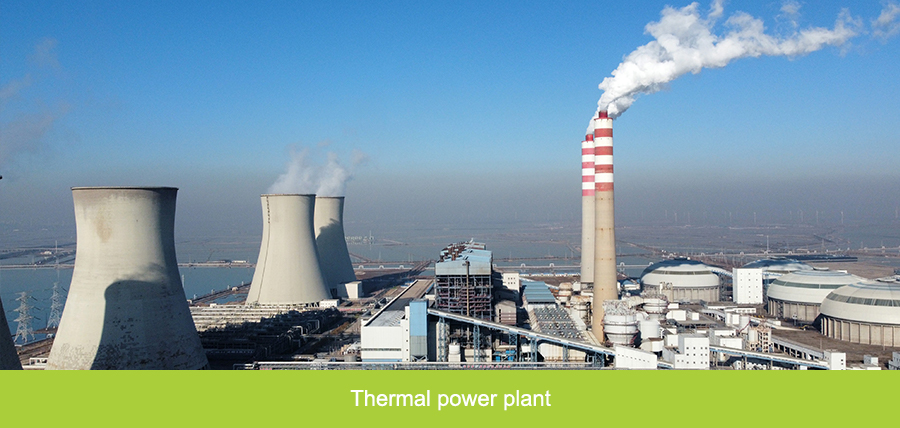
-
-
Surface preparation is crucial in coating construction. It ensures strong adhesion between the coating and the substrate, improving the durability and protective performance of the coating. By removing impurities such as grease, rust, and old paint layers from the substrate, issues like blistering and peeling can be avoided, extending the service life. At the same time, surface preparation eliminates unevenness, providing a smooth and uniform base for the coating, enhancing the appearance and overall performance of the coating. In short, good surface preparation is key to successful coating construction.
Table 1: The impact of various factors on the service life of the coating film
Factor Impact Degree (%) Steel surface rust removal treatment 50% Film thickness (number of coating layers) 19% Type of coating 5% Other factors (process, environment, climate, etc.) 26% Structural Treatment
The substrate itself must undergo certain treatments, such as grinding sharp edges, rounding off corners, removing splashes, and repairing and smoothing weld holes. These issues significantly affect the integrity and adhesion of the coating, so they must be addressed before rust removal.
Surface Cleaning
The substances harmful to the coating on the surface, such as oxide scale, rust, soluble salts, grease, and moisture, must be removed. If the surface preparation is not thorough, any residual impurities will affect the protective performance of the coating.
Surface Roughness:
Increased surface roughness enhances the contact area between the coating and the substrate, promoting mechanical bonding and improving the adhesion of the coating. However, roughness should not be excessive, as it may result in insufficient coating thickness at the peaks, causing early pitting. Deeper pits may trap air bubbles, which can lead to blistering in the coating.
- Surface Treatment Standards
-
When determining the extent of surface treatment, various standards must be referenced. The standards commonly encountered in practical work include national standards (GB), ISO standards, and North American standards.
Overview of National Standard GB/T8923
Part 1: Rust level and treatment grade of the surface of uncoated steel and steel surfaces after the complete removal of the original coating.
Part 2: Treatment grades for the surface of coated steel after partial removal of the original coating.
Part 3: Treatment grades for surface defects in welds, edges, and other areas.
Part 4: Initial surface conditions, treatment grades, and flash rust grades related to high-pressure water jet treatment.
Overview of International Standard ISO 8501
ISO 8501 consists of the following parts: General title, preparation of steel substrates before the use of coatings and related products—visual assessment of surface cleanliness:
Part 1: Uncoated steel and steel with completely removed coating rust.
Part 2: Pre-treatment of coated steel after partial removal of the coating.
Part 3: Pre-treatment of welded seams, edges, and other areas with surface defects.
Part 4: Initial surface conditions, pre-treatment grades, and rust removal grades for high-pressure water jetting.
Overview of North American SSPC/NACE Standards
The standards set by the Steel Structure Painting Council (SSPC) in the United States are also widely influential surface treatment standards.
Summary of SSPC-SP COM Surface Preparation.
SSPC-GUIDE TO VIS 1-89 Visual standards for sandblasted steel surfaces.
SSPC-GUIDE TO VIS 2 Standard evaluation method for the rust level of coated surfaces.
SSPC-GUIDE TO VIS 3 Visual standards for steel surfaces cleaned by power and hand tools.
SSPC-SP 1 Solvent cleaning.
SSPC-SP 2 Hand tool cleaning.
SSPC-SP 3 Power tool cleaning.
SSPC-SP 5/NACE 1 Abrasive blasting to a near-white metal surface.
SSPC-SP 6/NACE 3 Commercial abrasive blasting.
SSPC-SP 7/NACE 4 Brush-off blasting.
SSPC-SP 8 Acid cleaning.
SSPC-SP 10/NACE 2 Near-white abrasive blasting.
SSPC-SP 11 Power tool cleaning to a near-white metal surface.
SSPC-AB 1 Natural mineral and industrial waste abrasives.
SSPC-TR 1/NACE CG 1994 Technical reports on thermodynamic methods for steel surface cleaning.
- Oxidized Surface and Cleaning
-
Carbon steel has relatively weak corrosion resistance, so steel structures are prone to corrosion and rust formation. This depends on the surrounding environment, harmful components in the air (such as acids, salts, etc.), as well as temperature, humidity, and ventilation conditions.
1. The outer layer of rust is iron oxide, the middle layer is ferric oxide (Fe₃O₄), and the layer directly adhered to the metal surface is ferrous oxide (FeO), followed by a mixed metal oxide layer, which is a combination of FeO+Fe (the most difficult to remove).
2. Iron oxide is chemically stable, whereas ferrous oxide easily hydrolyzes into iron hydroxide under the influence of water and oxygen.
3. The oxidized surface may appear intact, but in reality, there are numerous gaps, where the hydrolysis and corrosion begin. The corrosion products cause stress on the oxidized surface, which leads to the peeling of the oxide layer.
4. Physical factors such as temperature changes and mechanical actions can also cause the oxide layer to lift or peel off.
5. The electrode potential of the oxide layer is 0.15–0.20V more positive than that of iron itself, which promotes iron corrosion as an anode in a corrosive medium.
Therefore, the oxide scale must be thoroughly removed before coating!!
Pretreatment
Surface pretreatment of steel involves cleaning the surface of oxidized skin, rust, and contaminants such as dust or dirt, typically through methods such as shot blasting or other techniques, before applying the primer in the painting workshop. It also includes removing any loose rust, slag, dirt, and dust from the surface of steel after primer or workshop primer application before applying corrosion-resistant coatings or decorative paints.
Solvent Cleaning
When solvent cleaning, special solvents should be used.
Wire Brush Cleaning
Wire brush cleaning is typically done using pneumatic or electric rotating wire brushes. This method is not suitable for removing the oxide scale but is effective for cleaning loose rust before treatment. If the surface is too smooth or if rust, oil, or dirt remains after cleaning, it will affect the adhesion of the coating and the overall effectiveness of the paint system. In such cases, further wire brushing should be done.
Surface pretreatment of steel involves cleaning the surface of oxidized skin, rust, and contaminants such as dust or dirt, typically through methods such as shot blasting or other techniques, before applying the primer in the painting workshop. It also includes removing any loose rust, slag, dirt, and dust from the surface of steel after primer or workshop primer application before applying corrosion-resistant coatings or decorative paints.
Chiseling Treatment
Manual chiseling or power tool chiseling methods for rust removal are typically used in conjunction with wire brushing methods. This method can also be applied to surface treatments of steel with existing paint films or local repairs of other paint systems. However, it is not suitable for surface pretreatment before applying epoxy or chlorinated rubber paints. This method is also useful for removing thick rust layers to make future abrasive blasting more economical.
Surface pretreatment of steel involves cleaning the surface of oxidized skin, rust, and contaminants such as dust or dirt, typically through methods such as shot blasting or other techniques, before applying the primer in the painting workshop. It also includes removing any loose rust, slag, dirt, and dust from the surface of steel after primer or workshop primer application before applying corrosion-resistant coatings or decorative paints.
Grinding with Abrasive Wheels
Grinding with abrasive wheels involves using pneumatic or electric rotating abrasive wheels to grind the steel surface to remove rust. This method is suitable for localized rust removal and welding seam treatments. It is an effective rust removal method and can achieve better results than wire brush cleaning or chiseling.
- Steel Plate Corrosion Grade
-
The corrosion grade of steel plates refers to the original condition of an unpainted steel surface, classified based on the degree of oxidation and rust. According to ISO 8501-1:1988, unpainted steel surfaces are divided into four grades (A, B, C, D), with corresponding photos for comparison.
Class A: Steel surface with a large area of adherent oxide scale, with almost no rust. Class B: Steel surface has begun to rust, and the oxide scale has started to peel off. Class C: Oxide scale has peeled off due to rust or can be scraped off, but only small pitting is visible on the surface. Class D: Oxide scale has peeled off due to rust, with widespread pitting visible on the surface. - Manual / Power Tool Rust Removal Grades
-
When manual tools are specified for cleaning, the contractor must ensure that the manual tool cleaning meets SSPC SP2 63 or equivalent standards. Manual and power tools such as scrapers, manual or power wire brushes, powered abrasive wheels, or grinding wheels should be used to remove thicker rust layers and clean off oil and dirt. After manual rust removal, the steel surface should be cleaned of any loose debris and dust. The rust removal grades are St2 and St3, generally used for steel surfaces without oxide scale. The descriptions are as follows:
St2: Thorough manual and power tool rust removal
When observed without magnification, the surface should be free of visible oil, dirt, and almost no loosely adhered oxide scale, rust, paint layers, or foreign matter. See photos B St2, C St2, and D St2.
St3: Very thorough manual and power tool rust removal
Similar to St2, but the surface treatment should be much more thorough, and the surface should have the shine of the metal substrate.
- Abrasive Blast Cleaning Grades
-
There are four grades for abrasive blast cleaning of steel surfaces that have undergone shot blasting or sand blasting. The descriptions of these grades are as follows:
Grade Description Sa1 Represents a light abrasive blast cleaning. The steel surface should be free of visible grease, dirt, and loose mill scale, rust, old paint layers, etc. Sa2 Represents thorough abrasive blast cleaning. The steel surface should be free of visible grease, dirt, and mill scale, rust, and old paint layers, with only firmly adhered residue. Sa2.5 Represents thorough abrasive blast cleaning. The steel surface should be free of visible grease, dirt, mill scale, rust, and paint layers, with only minor, dot-like, and streaky stains remaining. Sa 3 Represents a perfectly clean steel surface achieved by abrasive blast cleaning. The surface should be free of visible grease, dirt, mill scale, rust, and paint layers, and it should display a uniform metallic shine. - Common Surface Treatment Tools
-
High-Pressure Water Gun
High-pressure water gun rust removal is a method that uses high-pressure water to remove rust and contaminants from metal surfaces. The principle is to pressurize the water to a certain level and then spray it through a nozzle to impact and abrasive clean the rust, grease, dirt, and other contaminants from the surface. The nozzle can adjust the water flow's pressure and spraying angle to meet different cleaning requirements.
High-pressure water gun rust removal has several advantages. Firstly, it is environmentally friendly, requiring no chemical cleaning agents, which avoids harm to both the environment and workers. Secondly, the cleaning process is efficient and fast, saving time and labor. Thirdly, the water flow's impact is strong, reaching into cracks and complex areas to remove stubborn rust and dirt. Lastly, water gun rust removal does not cause significant damage to the metal surface, preserving the integrity of the material, making it suitable for large-area cleaning and long-term maintenance.
Dry Sandblasting Machine
Dry sandblasting rust removal utilizes high-speed abrasive particles to impact the metal surface, removing rust, grease, old paint, and other contaminants. The principle is to use compressed air to spray abrasive materials (such as quartz sand, steel grit, or aluminum oxide) at extremely high speeds. When the abrasives come into contact with the surface, they generate strong friction, removing the rust layer or contaminants. This process removes the surface oxide and roughens the metal surface, providing better adhesion for subsequent coating or anti-corrosion treatments.
Dry sandblasting rust removal has several advantages. Firstly, it provides an effective and quick rust removal, making it suitable for large surfaces and various complex-shaped workpieces. Secondly, the sandblasting process produces no liquid waste, avoiding environmental pollution and cleanup efforts. Thirdly, the sandblasting process does not cause significant damage to the metal surface, preserving its structural integrity. Finally, dry sandblasting equipment is easy to operate, and maintenance costs are low, making it an efficient, economical, and environmentally friendly rust removal method.
Self-absorption Shot Blasting Machine
The self-absorption shot blasting machine uses high-speed rotating shot blasters to shoot steel shots or other abrasive particles at high speeds to remove rust, oxides, oil stains, and other contaminants from the metal surface. Unlike traditional sandblasting, the self-absorbing shot blasting machine uses a self-suction design, where centrifugal force draws the abrasives into the machine and then evenly sprays them onto the workpiece surface. This process not only removes rust completely but also improves the metal surface's roughness, providing better adhesion for subsequent coatings or anti-corrosion treatments.
The advantages of self-absorption shot blasting machines include: First, excellent rust removal, able to quickly clean the surface contaminants, and suitable for various shapes and sizes of workpieces. Second, the noise level during operation is lower, and the process is dust-free, meeting environmental protection standards. Third, the equipment has a high degree of automation, significantly increasing production efficiency and reducing manual labor. Lastly, the efficient abrasive recycling system reduces abrasive consumption, lowering operating costs, making it an economic, eco-friendly, and efficient rust removal device.
Grinding Wheel Machine
Grinding wheel rust removal uses a high-speed rotating grinding wheel to mechanically grind the metal surface. The cutting action produced by the friction between the grinding wheel and the metal surface removes rust, oxides, oil stains, and other contaminants. The surface of the grinding wheel is typically composed of hard abrasive particles that provide enough cutting force when rotating at high speeds, removing rust layers or aging paint layers from uneven surfaces. Grinding wheel rust removal is suitable for smaller, more precise workpieces, especially areas that are difficult to clean with other methods.
The advantages of grinding wheel rust removal include: First, high rust removal efficiency, especially for handling smaller areas or precision parts of metal surfaces. Second, simple operation with low technical requirements, and relatively low equipment costs. Third, grinding wheels can adjust grinding force and speed, adapting to different rust removal needs. Finally, grinding wheel machines produce finer grinding effects on the metal surface, completing the rust removal task without damaging the material structure, ensuring surface quality and feasibility for subsequent processing.
-
-
How to Select the Right Coating Type?
We don't know where to start.
-
ISO 12944 is a standard developed for corrosion protection of steel structures by paints, determining the corrosive environment, anti-corrosion life, paint matching, and film thickness.
Choose
-
How to Solve Industry with Coatings?
Corrosion factors are numerous and varied.
-
We serve municipal engineering, chemical industry, power plants, steel structure factories, and wastewater treatment plants, with numerous successful cases and experience.
Experience