How to Coating?
Mengneng Coating Academy provides you with important considerations during the coating application process, which are especially crucial in construction and industrial settings. Coatings not only enhance the appearance but also protect substrates from corrosion and wear. The performance of coatings, such as corrosion resistance and waterproofing, can only reach their maximum effect through proper application methods. Key factors include surface preparation, coating selection, environmental control during application, and coating thickness. Scientifically standardized construction methods ensure both the aesthetic and durability of the coating, extending the lifespan of the item. In short, proper coating application is the key to ensuring coating performance and enhancing the overall value of the item.
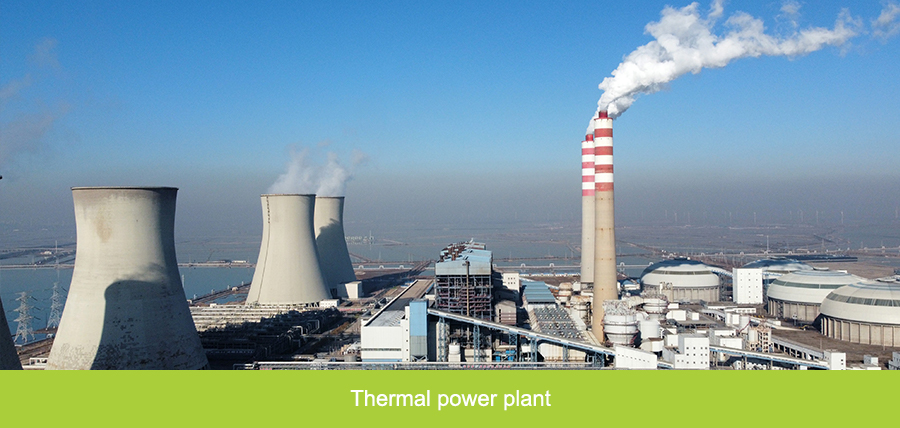
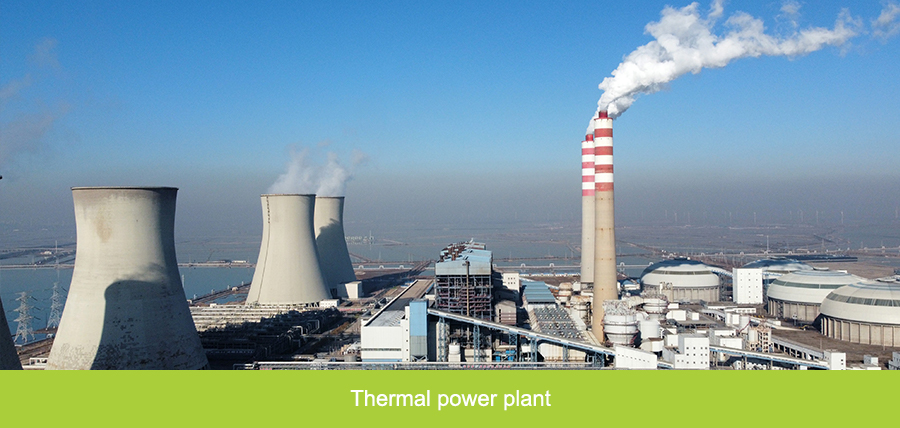
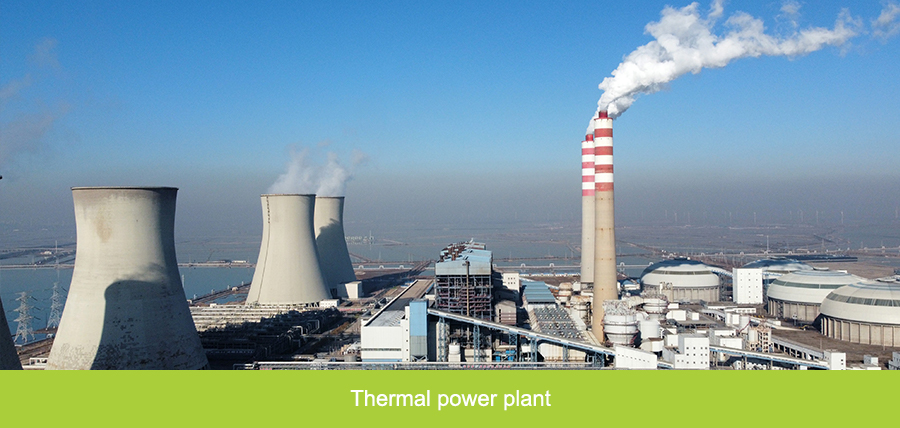
-
-
Painting Construction Specifications
Surfaces requiring coating: Surface treatment must be performed in strict accordance with the Steel Structures Painting Council (SSPC, USA) or other equivalent standards. Paint selection should be accurate, and the coating process must be followed diligently. The quality of surface treatment must be strictly inspected, and painting should not be carried out if the standard requirements are not met.
Painting applications should comply with the requirements outlined in this document. Restrictions during painting: If the painting is done at the contractor’s factory, the contractor must ensure the following conditions are met: proper surface cleaning has been done, the environment is dust-free, ventilation and lighting are adequate, and appropriate temperature and humidity conditions are maintained. For outdoor coating work, painting should not be carried out under harsh weather conditions, such as high humidity or strong winds, unless appropriate measures are taken to overcome these difficulties. Surface treatment and painting should only proceed if the temperature of the treated surface is at least 3°C above the surrounding air dew point. When painting, the temperature of the treated surface should be no lower than 7°C and no higher than 38°C.
- Precautions
-
A: Humidity Limitations
Weather Considerations
Painting should not be carried out under direct sunlight, or in rainy, snowy, or foggy weather. Painting should not be done when smoke is present or when the relative humidity causes condensation on the metal surface due to temperature fluctuations between the metal and the environment.
Unless otherwise specified by the paint manufacturer, painting should generally be carried out when the relative humidity is below 85%.
All surfaces should be completely dry before painting, during painting, and within 24 hours after painting.
B: Temperature Limitations
Consideration of Substrate and Ambient Temperature
Unless otherwise specified by the paint manufacturer, painting should generally be carried out when the temperature is between 10°C and 32°C. When the ambient temperature is below 5°C or if the temperature is expected to drop to 0°C before the paint dries, painting should not be performed.
Steel at temperatures above 50°C should not be painted unless specially formulated paints for high-temperature applications are used. When painting steel in hot climates, precautions should be taken to ensure that the specified dry film thickness is achieved.
Welding areas should be painted only 72 hours after welding.
Painting should only be carried out when the substrate temperature is at least 3°C above the dew point. Painting should not be performed when the surface is covered in condensation.
C: Time Limitations
Consideration of Interval Times
Generally, the primer should be applied within 4 hours after sandblasting is completed. If this period exceeds 4 hours, the surface must undergo a second treatment. This time limitation may be modified depending on the temperature and humidity conditions. The primary standard should be that no rust film should form on the surface before applying the primer. If any rust film is formed, the surface should be sandblasted again before applying the primer. The coating intervals should be strictly controlled according to the coating process.
D: Clean Air
Consideration of Dust Contamination
The surrounding air should be kept clean during the coating and drying process, and painting should not be carried out in dusty environments.
E: Mixing and Proportions
Consideration of Paint Ratios and Mixing
Paint mixing should be done strictly according to the manufacturer’s product instructions. The paint’s certificate of conformity should be strictly checked, and any unqualified or expired paint should not be used for coating. Before use, the paint must be mixed and stirred thoroughly to ensure it is well combined. When applying multiple layers of paint, each layer’s color should maintain enough contrast to facilitate checking whether the surface is fully covered.
F: Painting Methods
Consideration of Tools
High-pressure airless spraying, brushing, or compressed air spraying can all be used for application.
Brushing: The brush should be dipped in an appropriate amount of paint, and the paint should be applied to the surface evenly, first horizontally, then vertically, to ensure even coverage. Alternatively, the vertical application can be followed by horizontal brushing to avoid omissions.
Compressed Air Spraying: In this method, compressed air is used to pull (or force) the paint from a container into the spray gun, where it mixes with air and atomizes. The paint is then sprayed onto the surface, forming an even coating. The paint used for compressed air spraying is usually thinner than that used for brushing or rolling, and some thinner may be added to the general paint.
High-pressure Airless Spraying: This method uses a high-pressure pump powered by compressed air to pull and pressurize the paint to 10–25 Mpa, and then spray it through a nozzle with an olive-shaped hole. The paint is atomized into fine particles and sprayed onto the surface to form an even coating.
Other Requirements: To ensure the paint thickness at welds, edges, and corners, a pre-coat should be applied with a brush before performing large-area airless spraying.
-
-
How to Select the Right Coating Type?
We don't know where to start.
-
ISO 12944 is a standard developed for corrosion protection of steel structures by paints, determining the corrosive environment, anti-corrosion life, paint matching, and film thickness.
Choose
-
How to Solve Industry with Coatings?
Corrosion factors are numerous and varied.
-
We serve municipal engineering, chemical industry, power plants, steel structure factories, and wastewater treatment plants, with numerous successful cases and experience.
Experience